The effectiveness of pick-and-place machine feeders is primarily determined by their stability and throughput rate. In the industrial process, many machines have one or more critical components that are vital to their operation, and for pick-and-place machines, the key aspect is the throughput rate. Choosing and maintaining feeders is an essential part of daily operations.
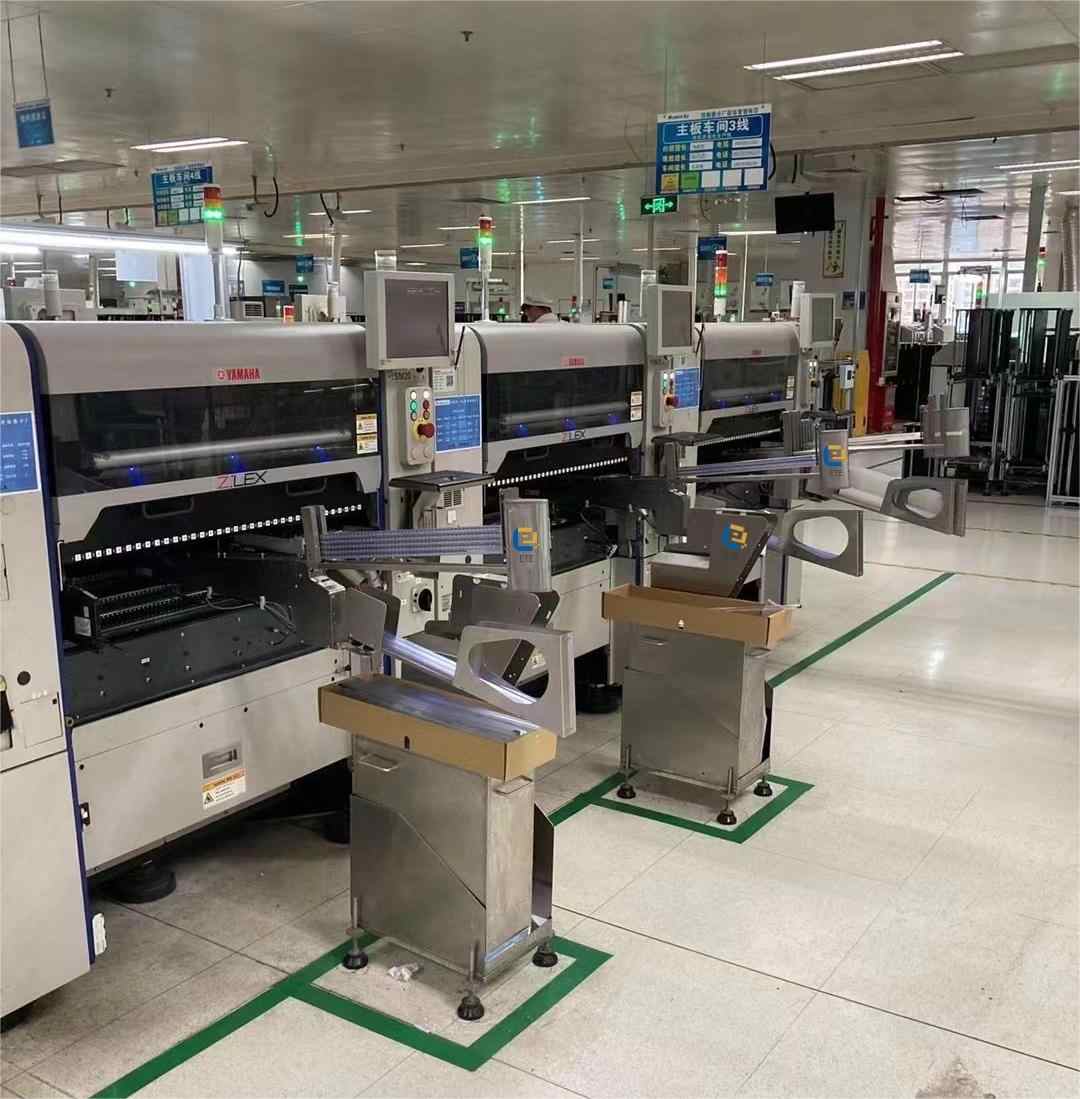
Importance of High Stability and Throughput Rate
A good feeder should exhibit high stability and throughput rates right from the point of purchase. This requires operators to conduct thorough testing and checks. The mechanical drive of the feeder relies on a cam spindle to drive the feeding mechanism, which rapidly strikes the feeder’s striking arm. This action moves the connected ratchet to advance the component tape while simultaneously driving the plastic roll to peel off the caps on the tape. The suction nozzle then descends to complete the pickup action.
However, due to the high-speed operation of the feeders, prolonged usage can lead to significant wear on the ratchet claws. If the claws cannot effectively drive the plastic roll to peel off the tape, the suction nozzle will fail to pick up components, thereby impacting the placement rate of the machine. Therefore, it is crucial to check the feeder thoroughly before installing the tape. Any worn ratchet claws should be repaired immediately, and those that cannot be repaired must be replaced promptly. Feeders that are not in use should be stored properly by designated personnel to prevent damage or accidents.
Pre-Installation Checks
Before installing the feeder, it is essential to clean the rotating bearing installation surface of any dust, chips, and debris to maintain cleanliness. Additionally, the feeder should be installed correctly and securely on the feeding platform, especially when height detection equipment is involved. Incorrect installation can lead to damage to the feeder or the equipment itself. Regular cleaning, washing, and lubrication are also necessary maintenance tasks.
Conclusion
Implementing these measures ensures both productivity and quality in operations. A reliable feeder is undoubtedly a core component of the pick-and-place machine, and its performance directly influences the overall efficiency of the machine.
At YEETAI, we produce all kinds of feeder to upgrade SMT machines.