Radial Lead Forming Machine: Advanced Automation for Efficient Component Processing
Our Radial Lead Forming Machine automatically forms radial capacitors in loose package. It comes with a computer motherboard control system, utilizing a vibrating bowl for automatic feeding. This machine features a robotic arm for material handling, shaping, polarity testing, directional sorting, lead cutting, and bending, all performed at designated workstations.
Key Features of Radial Lead Forming Machine
- User-Friendly Touch Screen Interface
The intuitive touch screen interface allows for easy parameter settings and monitoring, making operation straightforward. - Noise Reduction and Precision
The machine employs a left-right sliding seat and motor displacement mechanism, effectively reducing noise and enhancing transmission accuracy. - Compact and Portable Design
The machine features an integrated structure that is compact and easy to transport. The mold design is modular for quick and convenient replacements. - Customizable Molding Options
The forming method can be tailored to meet customer specifications regarding shape and size, ensuring flexibility in production. - High-Quality Components
The machine utilizes imported SMC cylinders and solenoid valves for durability. The forming molds and cutting tools are crafted from high-quality Japanese SKD-11 material, ensuring long-lasting performance. - Suitable for Various Products
This machine is ideal for processing electrolytic capacitors.
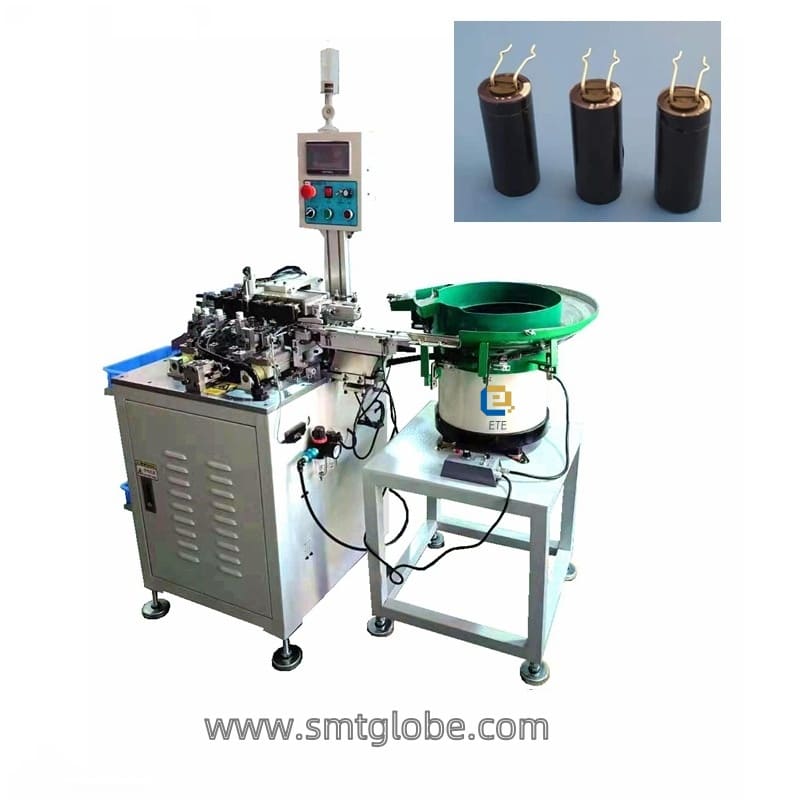
Additional Features of Radial Lead Forming Machine
- Adjustable Vibrating Bowl Speed
The speed of the vibrating bowl is adjustable and controllable, allowing for high-speed feeding and simple operation. - Automatic Component Sensing
The machine automatically detects when components are low and will trigger an alarm to notify the operator. - Precision Material Handling
The robotic arm automatically picks and feeds components with high precision. - Automated Testing and Disposal
The machine performs automatic testing and discards defective components, ensuring quality control. - Adjustable Forming Speed
The forming process speed is adjustable to meet production needs. - Touch Screen Control System
The easy-to-use touch screen control system simplifies operation and monitoring. - MES Interface Compatibility
The machine can be equipped with an MES (Manufacturing Execution System) interface for enhanced integration into production environments. - Customizable Forming Dimensions
We can customize the forming dimensions based on customer requirements, providing tailored solutions for various applications.
Machine specification:
Model: ETE-309QD
Tool Material: Japan SKD11
Sheet Metal Process: High-temperature powder spraying/surface anode/hard chromium
Power Supply: 220VAC/50HZ
Air Supply: 5-7mpa
Overall Dimension: L1450xW950xH1500mm
Weight: 380Kg
Processing Efficiency: 3000-4500pcs/H
Power Supply Voltage: 220 (V)
Feeding Method: Fully automatic feeding by vibration plate and mechanical hand clamping Adjustable lead length (mm)
Processing Capacity: 3000-4500pcs/H Adjustable bending dimensions
Conclusion
The Radial Lead Forming Machine is a cutting-edge solution for manufacturers seeking efficient and automated processing of radial components. With its advanced features, user-friendly interface, and customizable options, it is designed to meet the diverse needs of modern production lines.
For more information on how our radial lead forming machine can enhance your production process, contact us today or request a quote!
How to operate Radial lead forming machine?
I:Power on
1, Open the Radial lead forming machine power switch, light marking power. And the governor knob to zero, then open the feed switch.
2, the Radial lead forming machine plate on the governor knob to zero, and then open the vibration plate on the toggle switch, and will be adjusted to the appropriate speed position.
Second, cut the component lead
1, the components to be processed into the Radial lead forming machine vibration disk, and then open the feed switch and vibration disk switch and at the same time adjust the vibration knob and feed knob vibration size, so that the components can be carried out in the vibration disk, and smoothly through the interface on the track delivery.
2、Insert the air source and adjust the appropriate air pressure according to the size and weight of the component body.
3, adjust the capacitor molding machine track left and right distance, so that it does not affect the components travel, and does not need to be too wide, the width of the inner edge of the middle than the width of the components of 1-2mm. vibration plate interface to be smooth engagement with the foot cutting machine track.
4, adjust the height of the cut foot pressure strip, so that it is slightly higher than the component material 1-1. Smm.
5, adjust the capacitor molding machine knife box knob, against the ruler pointer, so that it meets the required foot length. And then open the capacitor molding machine cut foot
Switch, and try to cut 1PCS measurement size. When the foot length meets the requirement, it can be mass production.
Three: shutdown
1、When the components on the track have finished walking, turn off all the switches of the capacitor molding machine and remove the waste feet in the waste hopper.
2, wipe the Radial lead forming machine track and in the knife box oil hole point lubricating oil.
If you need more component lead cutting and forming machines, you may read contents as below.
Loose Axial Lead Cutter Former
Radial Lead Forming Machine ETE- 309QD
Radial Lead Cutter Former ETE-307G
Multifunctional Component Lead Cutter and Former ETE-0025
Radial Component Lead Former ETE-0020