Operating a radial insertion machine requires adherence to several important protocols to ensure efficiency, safety, and quality control. Know Radial Insertion Machine Guidelines from us. Below are key considerations for operators and quality control personnel during the operation process:
1. Material Storage and Organization
Materials should be organized according to machine type and batch size on designated racks. Ideally, items should be stored in a single layer. If stacking is unavoidable, additional racks are required, with clear labels indicating the customer, machine type, batch size, and stack level. Only specific personnel should handle material storage and retrieval, and appropriate logging must be maintained.
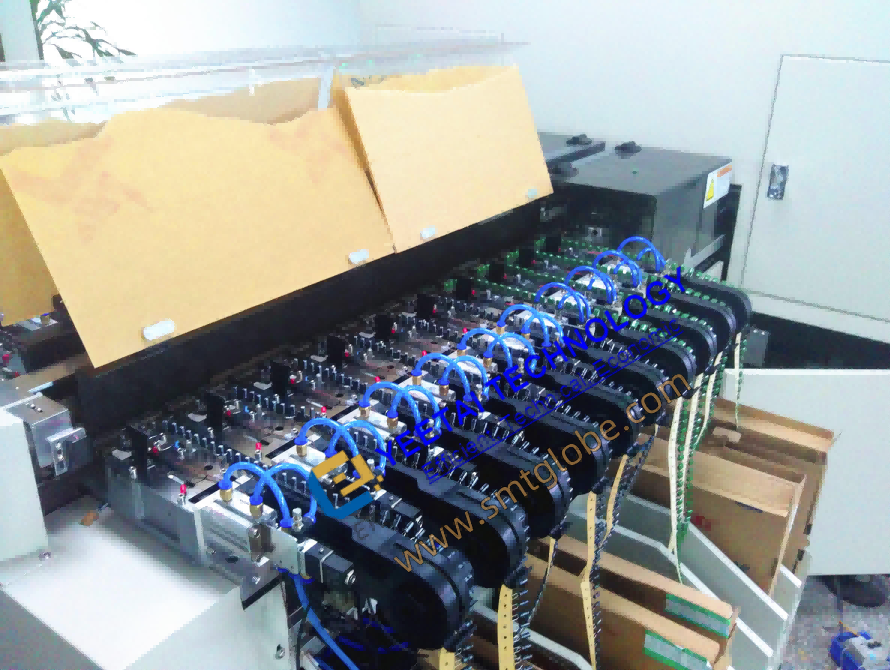
2. Loading Verification
Before loading materials, operators (RD personnel) must verify with the material loading checklist. After loading, they must call for quality assurance (QA) personnel to inspect the loaded materials. The machine should only be activated after confirmation and signature from QA.
3. Regular Line Inspections
QA personnel or designated loading staff should conduct unscheduled checks along the production line every 30 minutes. Special emphasis should be placed on ensuring that materials are not incorrectly or reversely loaded. If materials require a change during production, operators must prepare in advance to avoid machine downtime that can impact operational efficiency.
4. Manual Component Loading
During operation, RD personnel are required to carefully check the specifications, model numbers, and orientation of components when performing manual loading. Only when all aspects are confirmed as correct should manual loading be executed.
5. PCB Handling Precautions
To prevent scratches, PCBs must never be stacked together. This applies to boards that have arrived horizontally or those that have just been processed vertically. Transportation or storage should always utilize turnover carts or boxes.
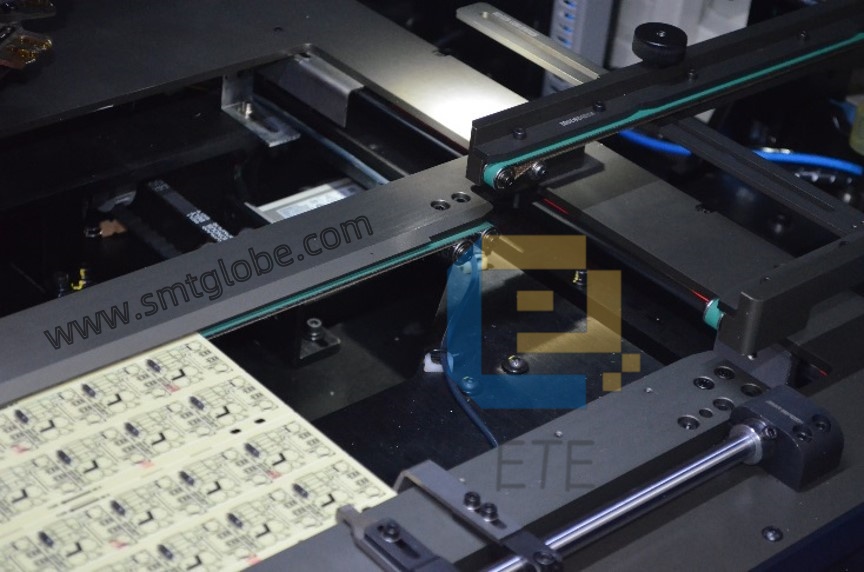
6. Addressing Defective Boards
If there is an increase in defective boards during production, operators must halt the machine immediately and request engineering assistance. Should defects arise from customer-supplied materials or operator error leading to broken, scratched, or edge-damaged PCBs, affected boards must be promptly reported to the team leader for necessary adjustments with the customer.
7. Cleanliness After Production Runs
Once a production run is completed, the operator should ensure that the machine, workstation, and surrounding area are thoroughly cleaned. Any leftover components should be confirmed and stored in designated containers to facilitate the quality control process of remaining boards.
8. Reporting Remaining Boards
At the end of a production batch, both operators and QA staff are responsible for identifying and documenting any leftover components in written form to report to the shift’s team leader. It is essential to avoid shifting blame; issues arising during the shift must be resolved by the current team.
By following our Radial Insertion Machine Guidelines, operators can achieve optimal efficiency while maintaining high standards of quality and cleanliness in the PCB production process. Adhering to these protocols not only enhances productivity but also ensures compliance with safety and quality regulations.
We can help to simplify and qualify your PTH PCB assembly process.
Feel free to contact us for more help.