In today’s fast-paced electronics industry, the reliability of printed circuit board assembly (PCBA) is crucial, especially for communication devices. With increasing demands for quality and performance, effective repair techniques become paramount. This article explores essential processes and common challenges in PCBA Rework.
1. The Significance of Preheating
Preheating is vital for successful Rework. Using an oven to preheat the board helps prevent the “popcorn” effect, a common issue when moisture-laden surface mount devices (SMD) are rapidly heated. This rapid temperature change can lead to internal cracking. Adequate preheating minimizes risks such as delamination, bubbling, and discoloration, particularly in thin PCBs, which are more susceptible to deformation and may face issues like BGA (Ball Grid Array) soldering problems.
2. Challenges with Large, High-Capacity PCBs
2.1 Issues Encountered
- Large boards absorb heat unevenly, increasing the risk of warping.
- BGA components may expand differentially, leading to shorts or cold solder joints.
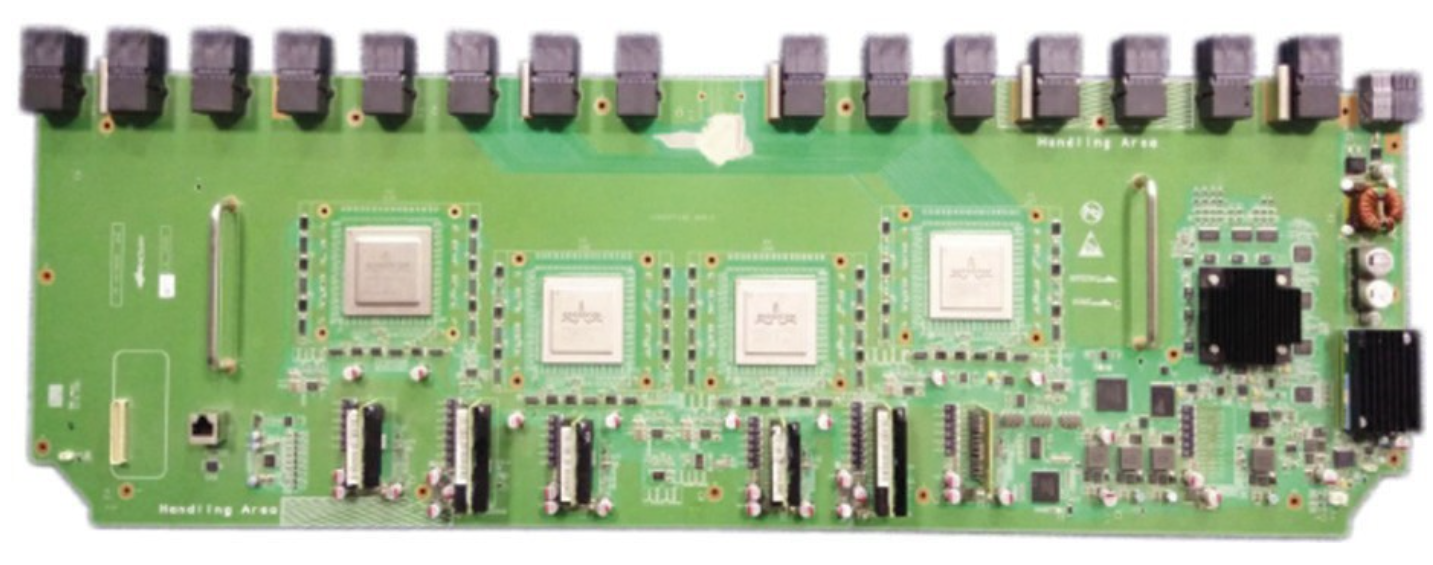
2.2 Solutions
- Ensure uniform preheating across the entire board to keep temperature differences within 10°C, especially around BGA solder points.
- Utilize supports or fixtures to reduce board deformation during the soldering process.
- Optimize solder stencil design to minimize opening sizes in BGA corners, thus lowering the risk of bridging.
3. Desoldering Techniques for Large PCBs
Traditional desoldering methods involve iron and solder wick, which can pose several risks. Prolonged contact with the iron may cause copper pads to lift or become damaged, especially on closely spaced pads typical of modern designs. Employing hot-air rework stations can mitigate these risks by providing controlled heat application.
4. Repairing PTH (Plated Through Hole) Components
For PTH repairs, small solder baths or immersion techniques are commonly employed. However, these methods can lead to new challenges, including solder joint reliability issues and potential short circuits if not managed properly.
5. Implementing Best Practices
- Use Proper Equipment: Investing in quality tools ensures precision and reduces the likelihood of damage.
- Train Technicians: Skilled workers can navigate complexities better, ensuring procedures are followed accurately.
- Adhere to Guidelines: Following established standards for PCB repair can lead to enhanced reliability.
Conclusion
PCB assembly repair is a critical aspect of maintaining the quality and performance of electronic devices. By understanding the essential processes, identifying potential challenges, and implementing best practices, manufacturers can ensure high standards of repair. This not only enhances product reliability but also extends the lifecycle of electronic components, ultimately benefiting both producers and consumers.
By focusing on these key areas, companies can improve their repair processes, keep pace with industry demands, and maintain a competitive edge.
PCBA rework must be correctly preheat the veneer before, at the same time, with the PCBA assembly density is getting higher and higher, device assembly more and more precise, need to consider automatic or semi-automatic rework methods. The traditional hand-held hot air gun or soldering iron to heat the PCBA is an uncontrollable process. This is because there is no telling what damage will be done to the board, the solder joints and what is around the solder joints. It is desirable to make more use of controlled process methods, with appropriate temperature profiles set, so that it is possible to know how the rework will affect the rest of the PCBA and what adverse effects it will have on the reliability of the board. In summary, the use of automatic and semi-automatic rework methods, the process strictly follow the IPC-7711/7721 standard rework procedures, and complete the relevant test and inspection steps, in order to achieve a reliable PCBA rework.
We can help to simplify and qualify your PTH PCB assembly process. We are also helpful at Through-hole process.
AI Spare parts
SMT AGV Robots
SMT cleaning solutions