Before different types of PCB Depaneling Machines enter production, there are various considerations that need to be addressed. To ensure stable operation and a smooth manufacturing process, let’s explore the essential preparations required for the most common types of cutting machines.
1. Movable Blade PCB Depaneling Machine
The Movable blade cutting machine uses an upper round knife and a lower flat knife to cut the PCB boards. The process begins by placing the board on the lower flat knife. Once the switch is activated, the upper round knife moves horizontally to the predetermined cut point, slicing through the V-cut PCB board without leaving any rough edges.
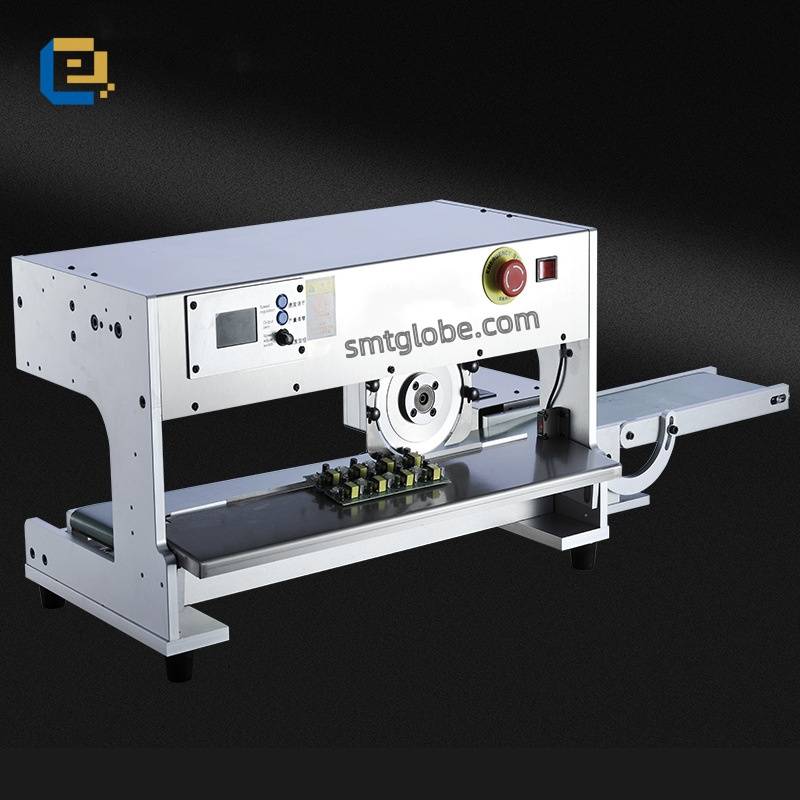
Key Considerations:
Read the Manual: Familiarize yourself with the operating steps detailed in the instruction manual.
Safety First: Do not remove the blade guard; safety is paramount.
Use the Right Material: This machine is specifically designed for V-cut circuit boards; avoid cutting other types of materials.
Wear Appropriate Clothing: Operators should wear fitted clothing and secure long hair to prevent entanglement.
Initial Setup: Insert the footswitch, check the voltage, and then power on the machine.
Test Run: Conduct a trial run for 2 to 3 minutes to ensure smooth operation.
Inspect Safety Features: Check that the infrared safety light curtain operates correctly.
Adjust Cutting Parameters: Set the cutting stroke and speed according to the depth of the V-slot and the thickness and hardness of the board.
Speed Settings: Experienced operators can use high speed; beginners should start with low speed.
The guillotine cutting machine is designed with a light structure powered by both pneumatic and electric systems. It efficiently cuts through thin boards with minimal shear stress, preventing bowing and micro-cracks, making it ideal for delicate and precise cutting tasks.
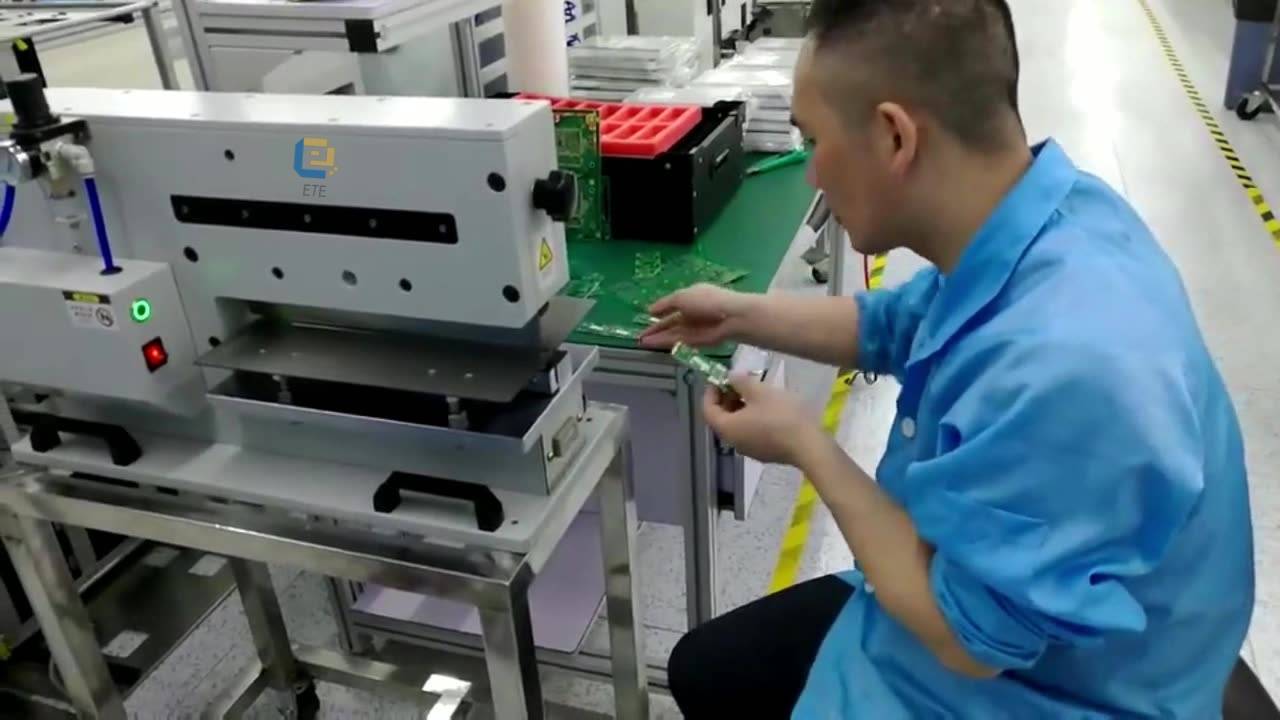
Key Considerations:
Operator Safety: Hand protection is mandatory; keep hands and body clear of the cutting area.
Check Connections: Ensure that the power supply is connected, and the air pressure is stable before starting the machine.
Align the Blades: Before cutting, ensure that the upper and lower blades are perfectly aligned to minimize burrs and extend tool life.
Confirm V-Slot Positioning: Verify that the V-slot on the board aligns with the cutting edge and remains fixed in position.
Designed Use: This machine is expressly for V-cut boards; avoid cutting other materials.
Blade Adjustment: Adjust the distance between the upper and lower blades based on the V-slot depth.
Grounding Safety: Install a grounding wire to prevent electric shock hazards.
3. Offline Visual Cutting Machine
Also known as a fully automatic cutting machine, the offline visual cutting machine utilizes a high-speed electric spindle combined with milling or round knives. It requires manual loading and unloading, cooperating with a CDD visual automatic system for faster processing of PCB boards.
Key Considerations:
Device Inspection: Before starting, check that the power and air supply meet operational requirements.
Safety Features Validation: Verify the operation of safety mechanisms, including emergency stop buttons and safety light curtains.
Tool Check: Inspect the cutting tools for alignment and replace any worn components promptly.
Training: Provide operators with training on both equipment and software to ensure they can quickly become proficient. Emphasize software operation and troubleshooting.
Correct Power Supply: Use the manufacturer-specified power type for stability and install grounding wires to prevent electrical hazards.
Tool Replacement Training: Operators should learn the methods for exchanging tools and related components.
4. Inline Visual Depaneling Machine
Key Considerations:
Connection Check: Confirm that the inline cutting machine integrates well with the production line, including electrical connections and external cleanup devices.
Equipment Inspection: Verify the functionality of the CCD visual system, computer systems, cutting devices, supply mechanisms, signaling devices, network connections, and MES systems.
Trial Runs: Perform trial runs to ensure smooth transitions through each stage: loading, cutting, and unloading.
Blade Inspection: Thoroughly check the cutting blades for wear and rigidity before operation.
Safety Verification: Failing safety mechanisms, such as emergency stop buttons and infrared sensors, should be promptly addressed.
Training Provision: Comprehensive training on equipment operation is necessary for operators to reduce human errors during automated processes.
Note on Tool Life: Operators should monitor the longevity of blades and other consumables throughout production.
Conclusion
Preparing different types of PCB Depaneling Machines for production requires thorough inspections, safety precautions, and appropriate training. By following these guidelines, manufacturers can ensure efficient operations and high-quality results in PCB production.
We are experienced at PCB depaneling. Know more PCB depaneling solutions in our website: www.smtglobe.com
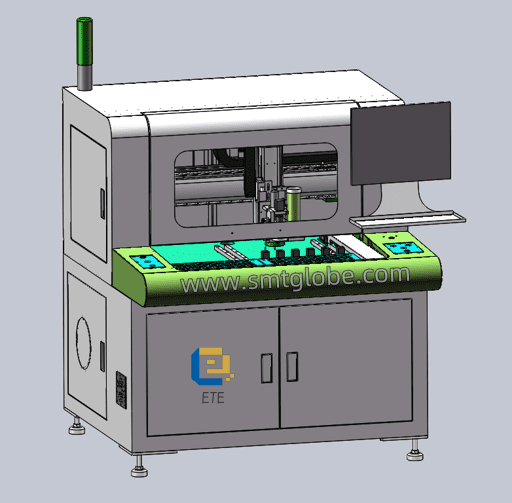