Maintaining the spindle of a router PCB depaneling machine is crucial for ensuring optimal performance and longevity. Below are detailed steps and considerations for effective maintenance.
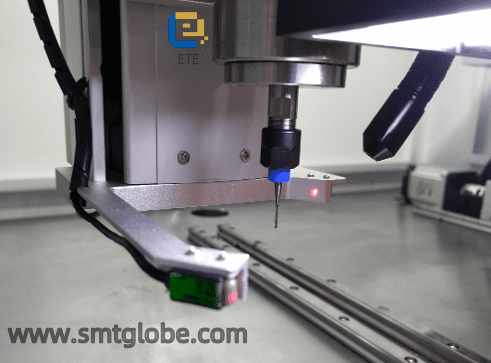
1. Confirm Spindle Speed
The spindle speed of the router PCB depaneling machine should typically range from 5,000 to 80,000 RPM. Regularly verify that the spindle operates within these parameters for consistent cutting performance.
2. Understand Cutting Performance
Familiarity with the machine’s cutting performance is essential. Key specifications include:
- Axis Movement Speed: Up to 1,000 mm/s.
- Cutting Speed: Adjustable from 1 to 100 mm/s, enabling flexibility for different materials.
- Repeat Accuracy: Less than 0.02 mm for straight lines, curves, and arcs.
3. Maintenance of the Router PCB Depaneling Machine
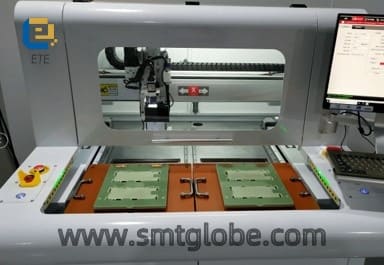
Proper maintenance practices should include the following:
- Spindle Bearings: Ensure that the spindle bearings are of high quality, typically made from ceramic and steel for durability.
- Tool Replacement: Tools should be replaced every 100-300 meters of cutting, depending on the PCB material, thickness, and the diameter and quality of the milling cutter used.
- Filter Bag Replacement: Replace the filter bag every 1,200-1,800 meters to maintain effective dust and debris collection.
- Dust Collector Monitoring: The dust collector features a self-checking function. Alarms will notify the operator when the filter bag is full, indicated by both auditory and visual signals.
- Safety Features:
- The machine is equipped with multiple safety features, including:
- E-axis stop, spindle stop, and cover stop.
- Dual emergency stop buttons at both the front and rear.
- The machine is equipped with multiple safety features, including:
4. User Manuals and Alarms
Understanding the machine’s alarm systems is vital for quick troubleshooting:
- Red Light: Indicates critical issues such as spindle head malfunctions, servo or PLC failures, or low air pressure.
- Yellow Light: Signals various non-critical conditions, including teaching mode, standby status, feeding board problems, mark point recognition failures, safety door openings, broken tools, and abnormal dust collector conditions.
- Green Light: Indicates the machine is in normal operating mode.
5. Safety Precautions
Ensuring a safe working environment is paramount. Implement the following safety measures:
- Fully Enclosed Working Environment: This minimizes exposure to moving parts.
- Safety Door Sensors: These ensure that the machine stops when doors are opened.
- Locks on Maintenance Doors: Safety locks on infrequently opened inspection and maintenance doors prevent accidental operation.
- Overload Protection: The machine is equipped to handle servo overloads, ensuring the spindle stops and the dust collector detects abnormalities.
By following these maintenance guidelines, operators can ensure the efficient and safe operation of router PCB depaneling machines, ultimately contributing to improved productivity and reliability in PCB manufacturing. Proper maintenance not only enhances performance but also extends the lifespan of the machinery, reducing long-term operational costs.
We are experienced at PCB depaneling. Know more PCB depaneling solutions in our website: www.smtglobe.com
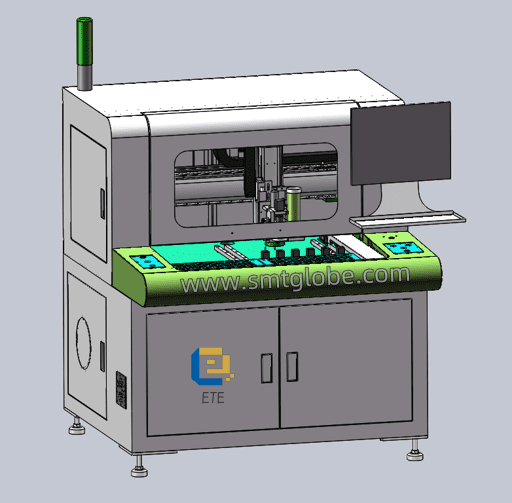