Efficient and precise PCB depaneling is crucial in the manufacturing process to ensure high-quality production. A PCB depaneling machine streamlines this task, and understanding its operation and workflow is vital for ensuring optimal performance.
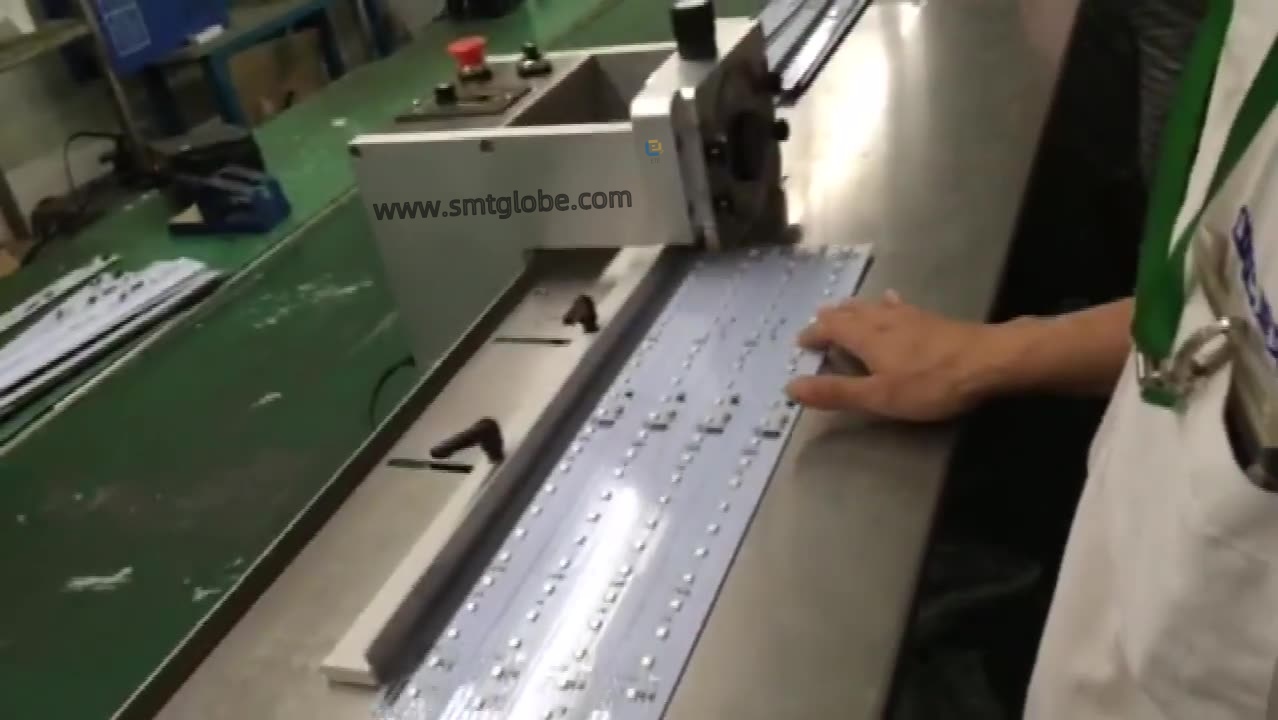
Pre-Operation Preparations
Before operating the PCB depaneling machine, certain necessary preparations must be made:
- Check Power Supply: Ensure that the power supply is stable and functioning properly.
- Inspect Supporting Equipment: Confirm that all accompanying equipment related to the depaneling machine is operational. This includes checking the machine’s spindle, fixtures, and system software.
PCB Depaneling Process
1. Initial Machine Setup and Inspection
- Once the pre-checks are completed, the operator should correctly orient the PCB and position it on the designated depaneling fixture.
- When placing the PCB, use your palm to gently press down, ensuring it fits securely in the fixture. Then, close the fixture’s cover tightly.
- With everything in place, the operator presses the green feed button located on either side of the machine. This action will automatically move the work table to the depaneling position.
- Next, click the appropriate button in the software, which will turn red for inspection. During this inspection phase, the operator must check that all cutting positions are correct. Once the inspection is complete, the work table will automatically retract.
- After confirming that everything is correct, press the stop button in the software. The button will display red, and after a few seconds, it will change to green, indicating readiness for operation.
2. Beginning the Depaneling Process
- With preparations complete, the operator initiates the production process by clicking the designated button in the software. This action will activate the depaneling machine, including the vacuum cleaner, spindle, and static eliminator.
- During pneumatic operation, after the template check is completed, there will be a startup waiting period for the spindle. In continuous processing mode, this waiting period is not required.
- While the PCB depaneling machine is in operation, attention must be paid to ensure that the cutting positions are accurate. If there are any misalignments or deviations from the correct cutting positions, the operator can immediately stop the machine by pressing either of the two red emergency stop buttons located on the left and right sides of the machine. After stopping, it’s essential to consult an engineer to resolve the issue before resuming operation.
3. Automated Production Cycle
- Once the PCB depaneling machine has completed cutting the PCB, the work table will automatically retract. The cut PCBs must all meet quality standards; if any defective products are identified, the operator should consult with an engineer to adjust the milling tool path as necessary.
- After confirming that the cut PCBs are compliant, the operator can safely remove the finished products and prepare to load new PCBs into the fixture. As before, gently press down with the palm to ensure proper placement and then securely close the fixture cover.
- Finally, press the green feed button again to allow the work table to automatically return to the depaneling position, continuing the production cycle.
Conclusion
Mastering the PCB depaneling process is essential for ensuring high-quality manufacturing. By following these outlined procedures, operators can effectively manage and optimize the performance of the PCB depaneling machine, ultimately leading to improved productivity and reduced operational errors. Proper setup, attentive monitoring during processing, and quick responses to issues will enhance the overall efficiency of PCB depaneling operations.
We are experienced at PCB depaneling. Know more PCB depaneling solutions in our website: www.smtglobe.com
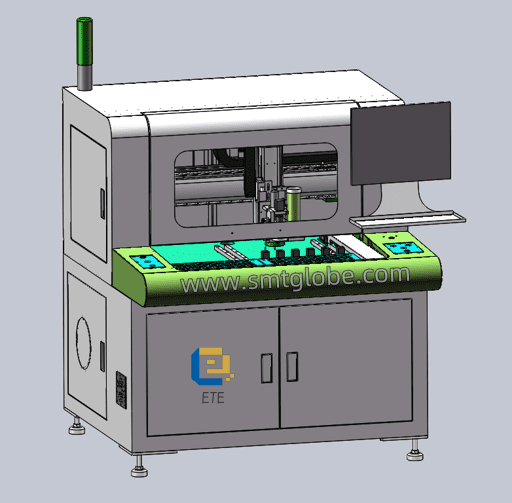