In the assembly process, there is often a lack of effective synchronization between information systems and the actual data from the assembly site. This results in poor timeliness of information transfer and a lack of transparency regarding the assembly status. Consequently, it becomes challenging for assembly units and processes to meet the actual needs of the site. Therefore, it is essential to implement measures that ensure real-time and accurate data collection from the assembly floor.Let us help you to enhance management and traceability in the PCB assembly process.
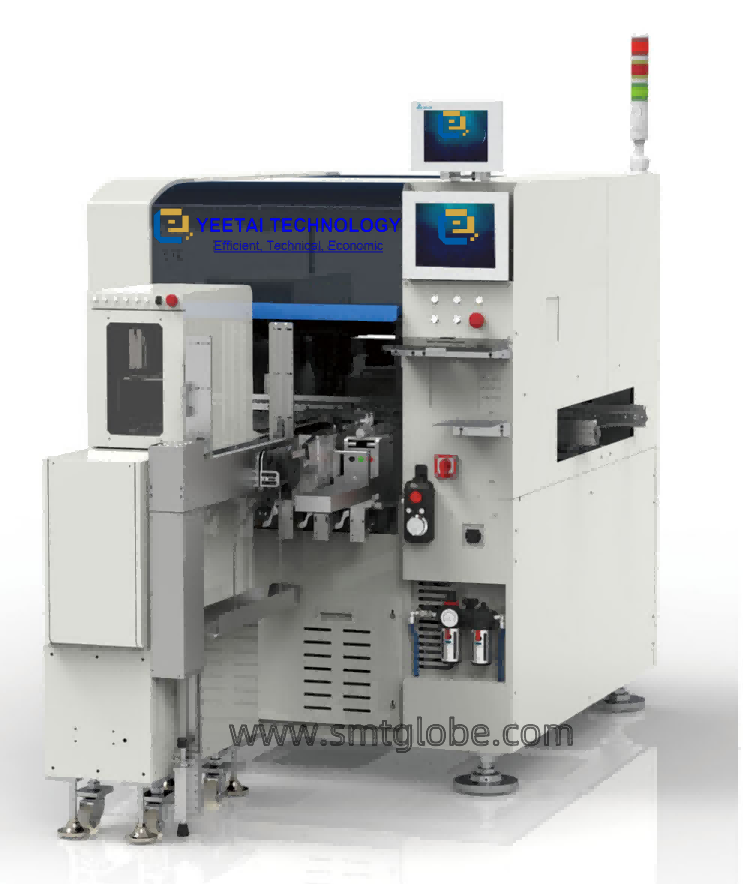
Current Data Collection Methods
There are three main types of existing data collection methods:
- Manual Data Input: Data is collected manually by workers, which can lead to inaccuracies and delays.
- Direct Data Acquisition from Production or Testing Equipment: This method allows for automatic data retrieval from machines, enhancing precision and efficiency.
- Automated Recognition Technologies: Techniques such as barcodes and RFID (Radio Frequency Identification) are utilized for data collection, offering a more streamlined and accurate approach.
Importance of Real-Time Data Analysis
Once real-time data is collected, analyzing and predicting this data is crucial for the digital and intelligent management of the odd form insertion machine assembly shop. Key areas of analysis include:
- Operational Status Analysis and Prediction of Assembly Production Lines: This helps in understanding how well the assembly lines are performing in real-time.
- Production Progress Monitoring: By analyzing the current status of production processes, managers can make informed decisions to optimize workflow.
- Equipment Fault Diagnosis and Prediction: Real-time data allows for proactive maintenance, reducing unexpected downtimes.
- Material Tracking and Management: Effective management of materials ensures that the right components are available when needed.
Precision Material Delivery
Currently, the production of odd form insertion machines is characterized by considerable unpredictability in material demand. The material supply department often prepares materials based on maximum demand levels. This approach leads to:
- Reduced Line-Side Space: Over-preparation of materials results in space constraints and significant material accumulation.
- Material Shortages: Despite high inventory levels, unexpected shortages may still occur.
To address these challenges, effective material delivery and path planning is necessary. This involves:
- Guided by Production Planning: Material delivery must be aligned with actual production conditions, ensuring efficiency and timeliness.
- Meeting Constraints: Delivery plans must satisfy constraints related to materials, time, and transportation capacity.
- Transport Equipment and Pathways: Determining the appropriate transport equipment, movement paths, delivery times, and speeds ensures that materials arrive at designated workstations promptly and in the required quantities.
Conclusion
Real-time data collection and analysis are vital for the success of odd form insertion machine assembly. By implementing efficient data acquisition methods and sophisticated analytical techniques, manufacturers can improve operational transparency, enhance decision-making, and optimize material delivery processes. This ultimately leads to more efficient assembly operations and a smoother production workflow. For organizations looking to excel in modern manufacturing, adopting these strategies is not just beneficial—it is essential.
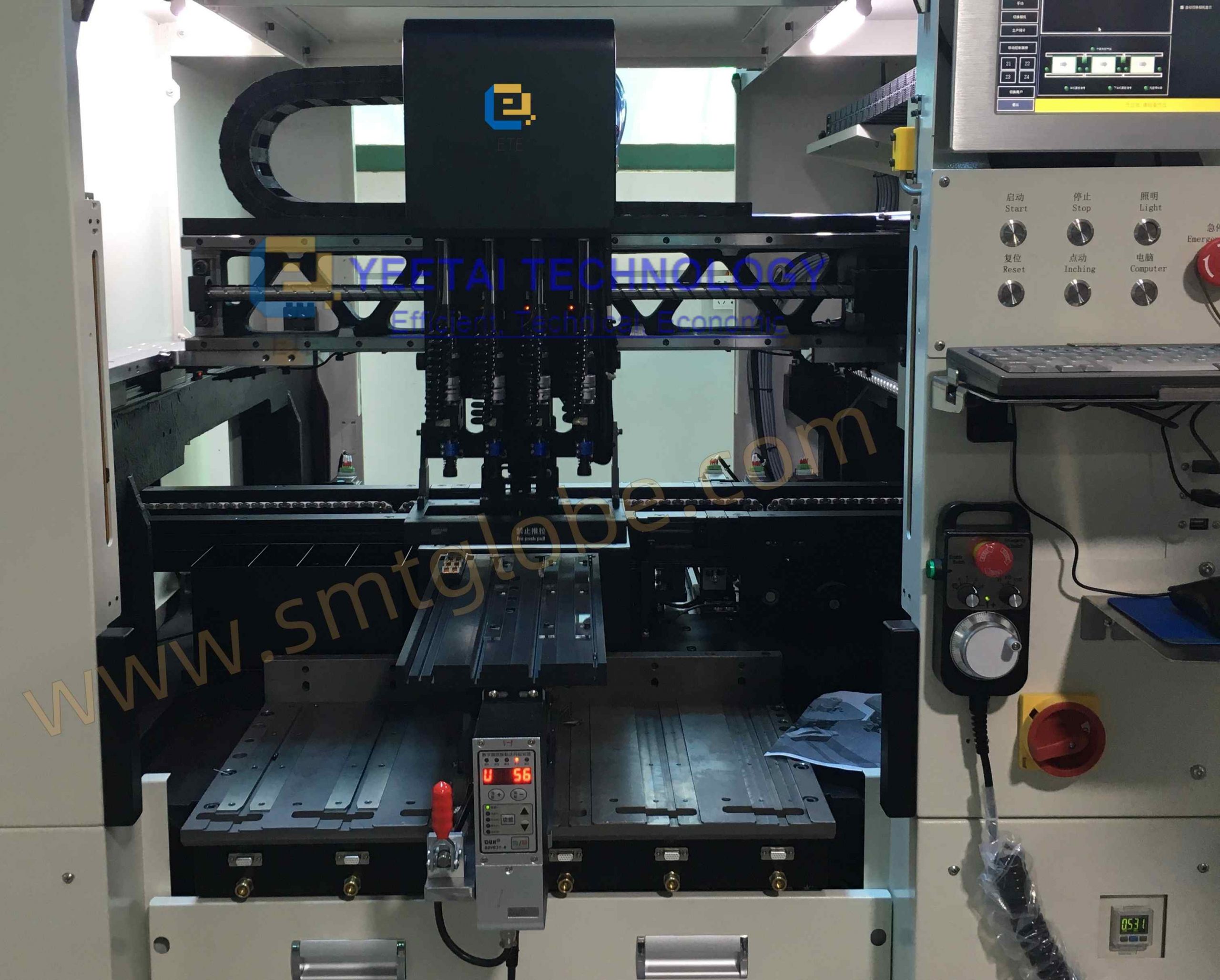
We can help to simplify and qualify your PTH PCB assembly process.