Flexible printed circuits (FPC), made from flexible copper-clad laminate, serve as vital components in electronic products, offering advantages such as high wiring assembly density, excellent bendability, lightweight design, and flexible manufacturing processes. FPCs can be classified into single-layer, double-layer, multi-layer, and rigid-flex circuits.
In the automotive sector, especially with the rise of new energy vehicles (NEVs), FPCs play an increasingly significant role. Both conventional and electric vehicles utilize FPCs extensively in their electronic systems. Automotive electronics encompass various control systems, including engine control, chassis control, and overall vehicle electronic control. Given the structural and spatial constraints in modern vehicles, FPCs are set to replace traditional wiring harnesses in many applications, particularly in smart vehicles.
Key Applications in New Energy Vehicles
NEVs often feature more than 100 individual FPC applications. The most critical areas include Battery Management Systems (BMS), vehicle lighting systems, door control systems, and camera modules.
The application of FPCs in BMS is particularly noteworthy. As battery costs and space efficiency become paramount, FPCs can optimize these factors effectively. With battery capacity nearing its limits, the quest for efficient structural designs highlights the need for innovative solutions. By utilizing FPCs instead of traditional BMS wiring, performance stability is maintained while reducing the risk of mechanical issues due to misalignment or friction caused by oversized components. In the long term, the trend may extend to using chips embedded in FPCs to further enhance stability and save space, despite current cost considerations not yet favoring this shift.
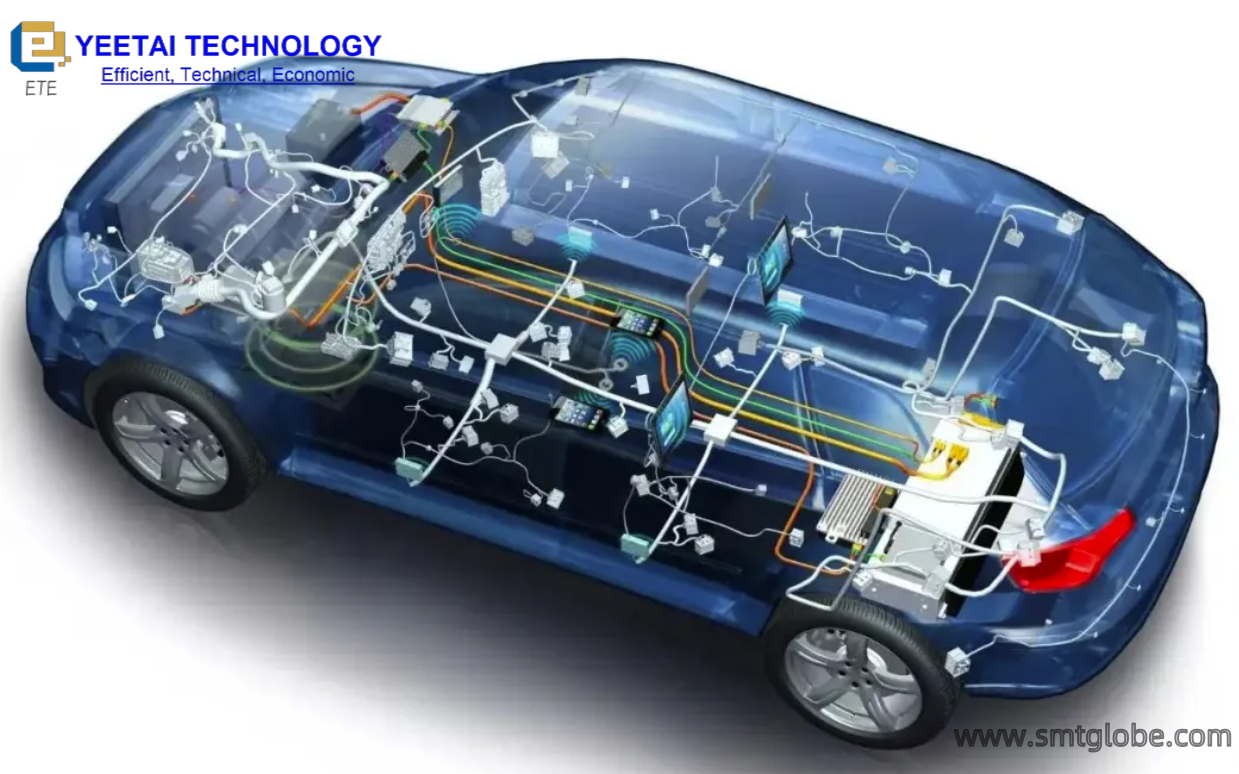
Advantages of FPC in BMS Applications
- Integration: FPC designs can integrate fuses, connectors, NTC thermistors, and aluminum/nickel terminals, providing high electrical performance while meeting the design demands for smaller and denser installations. This integration supports customization to meet specific structural requirements in battery packs.
- Automation: The assembly process benefits from quick and precise integration. FPCs significantly reduce the errors typically associated with traditional wiring harness designs. Automated soldering of FPCs to battery busbars minimizes labor costs and enhances manufacturing efficiency.
- Compactness: With a line thickness as low as 0.34 mm and an NTC thickness of 2 mm, FPCs allow for flexible assembly options, including bending up to 90° or 180°. This flexibility is crucial for fitting within the constraints of new vehicle designs.
- Lightweight: FPCs can reduce the overall vehicle weight by approximately 1 kg compared to traditional wiring harness solutions, positively impacting efficiency and performance.
- Cost Efficiency: Although the initial cost of FPCs may not offer significant advantages, the overall connection costs can be drastically reduced, leading to long-term savings.
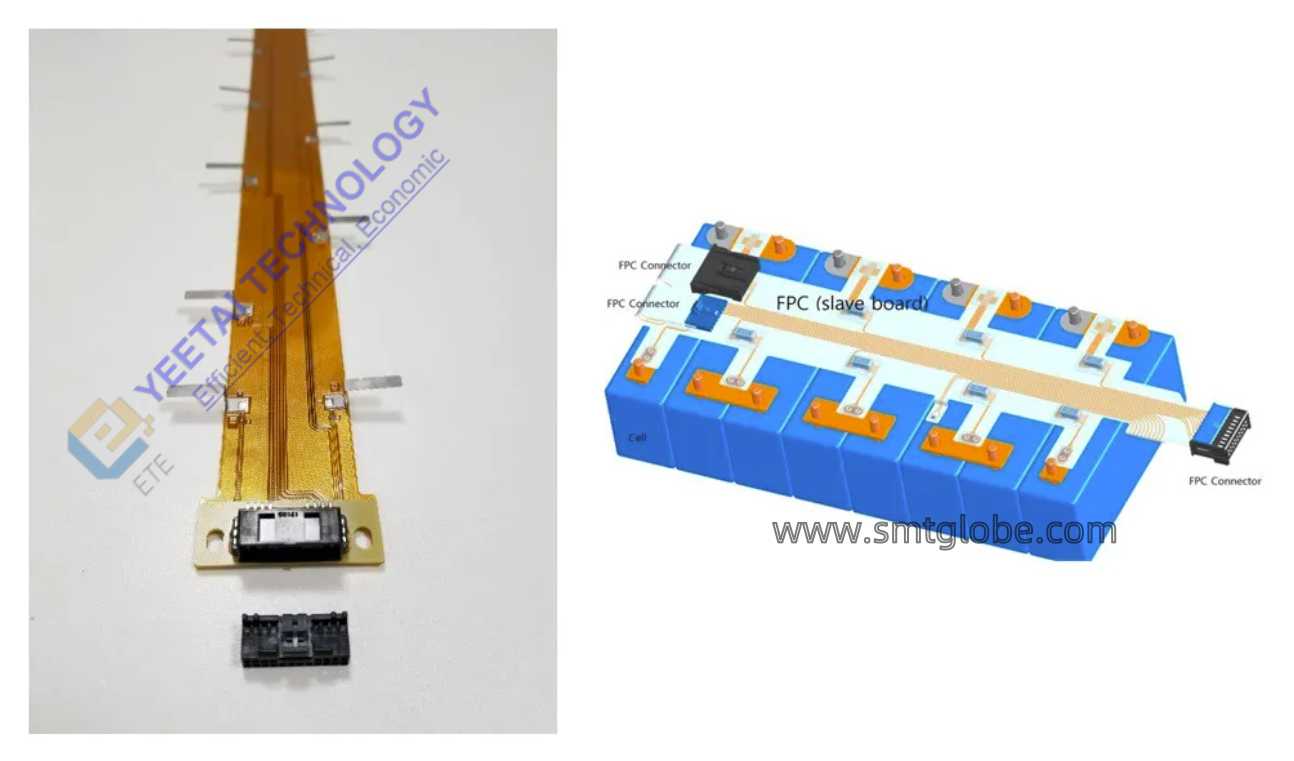
Trends
Currently, FPC solutions have become the primary choice for most new models of electric vehicles. The integration of FPC into Cell Contact Systems (CCS)—comprising FPCs, plastic components, and copper-aluminum busbars—highlights this trend. CCS products facilitate the efficient connection of multiple battery cells through laser welding, with FPCs providing essential electrical connections and signal detection capabilities.
In summary, the application of flexible printed circuits in new energy vehicles is a critical advancement, promoting efficiency, automation, and high-density design for the future of automotive technology.
We can help to simplify and qualify your PTH PCB assembly process. We are also helpful at Through-hole process.
AI Spare parts