The LED Vacuum Unloader,comes with a trolley. Designed for receiving 1.5m LED panels, this unloader simplifies the collection of LED boards from the upstream machine using an attached roller conveyor. Then the unloading machine pushes boards into the trolley. It allows operators to easily remove the full trolley from the rear end of the machine. This space-saving solution is ideal for handling long LED boards efficiently.
Features:
- The control panel features a user-friendly “touch screen” interface, making operation intuitive and efficient.
- The LED Vacuum Unloader comes with a PLC program control system and offers selectable pitch settings for precise and customizable operation.
- The flexible stocker car is for easy transportation and adaptability to different production needs.
- A servo motor drives the lifting platform and it ensures smooth and precise movement of PCBs.
- Operators can easily exchange the stocker car from the rear of the machine, facilitating maintenance and workflow adjustments.
- PCBs are smoothly transferred using durable rollers, minimizing the risk of damage during transportation.
- The stocker car can be manually placed and securely clamped in position, ensuring stability during operation.
- The LED Vacuum unloader is SMEMA compatible, allowing for seamless integration with other equipment in the production line.
Specifications
Transfer direction: L to R.
Conveyer type and speed: Stainless Roller; 0.5-20m/min adjustable
Air supply& consumption: ≥6 bar,10 ltr/min max.
Power supply:110V /220V, 50 Hz/ 1 Ph
Model | Dimension (L*W*H.MM) | PCB size (MM) | Weight (KG) | PCB Thickness |
SVUL330 | 1700 x 1700 x 1420 | 500*150~1500*500 | 220KG | 0.6mm ~ 4.0mm |
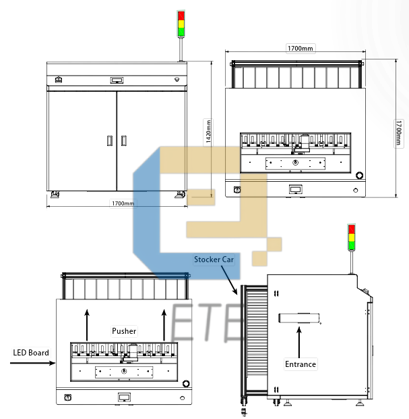
Operational manual
Before using LED Vacuum unloader, make sure the equipment is in an appropriate working environment. The work area should be dry, clean, and well-ventilated. Avoid using the equipment in dusty or humid environments to prevent affecting the vacuum suction effect and the stability of the device.
When installing the machine, ensure it on a stable tabletop or workbench. Ensure that the bottom of the equipment is in close contact with the tabletop, without any shaking or instability.