JUKI pick-and-place machines are widely selected by SMT (Surface Mount Technology) companies due to their performance and versatility. Popular models currently in use include the JM-100/20, KE-3010A, RS-1R, and RX-7R. This article will provide an overview of these models and highlight important operational considerations for users.
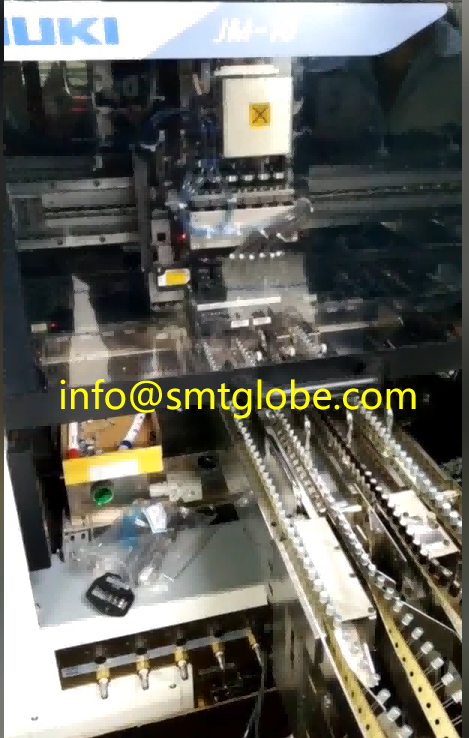
JUKI Pick-and-Place Machine Models
JUKI JM-100/20
The JUKI JM-100/20 is designed for handling large components and substrates. Featuring advanced MI solutions, this model significantly enhances insertion speed—accommodating component placement in just 0.6 seconds for suction nozzles and 0.8 seconds for clamp nozzles. This model is versatile, capable of efficiently producing a wide range of products from small to large components. Additionally, JUKI’s unique laser and vision recognition technology facilitates high-speed and high-precision identification of parts. Coupled with the JaNets software, it allows for comprehensive network connectivity throughout the manufacturing process, leading to improved quality, productivity, and management information visualization.
JUKI KE-3010A
The JUKI KE-3010A is suited for chip components and boasts impressive specifications. It can achieve up to 23,500 components per hour (CPH) under optimal conditions using laser recognition, and 18,500 CPH according to IPC 9850 standards. This model supports a range of components, from 0402 (imperial 01005) chips to 33.5mm square components and is equipped with 1 laser placement head and 6 nozzles. It utilizes an electric dual-track feeder that can carry up to 160 different components, enabling a flexible, high-speed, and high-quality automated production line.
JUKI RS-1R
The JUKI RS-1R combines functions of chip and general-purpose machines with line balancing capabilities. It accommodates a wide variety of components, ranging from size 0201 to 74mm, and can handle a maximum component height of 25mm. This model optimizes production output by achieving ideal line balance. The recognition position can adapt according to the component type, and JUKI’s advanced laser and vision recognition technology ensures high-speed and high-precision identification of parts. The machine can handle substrate sizes of up to 1200x370mm, 650x370mm (1 buffer), and 360x370mm (3 buffers).
JUKI RX-7R
The JUKI RX-7R is designed for small components, accommodating chip sizes from 03015 to 25mm square components. It features a P16 nozzle placement head for high-speed, dense placing of tiny components, and a P8 nozzle for fast, high-precision placement of medium-sized common components. Its compact width of 998mm saves valuable floor space and allows for dual-track production. The combination of placement heads can be optimized based on the product type, and its unique planetary placement head design achieves one of the highest production performances in the industry, reaching up to 75,000 CPH.
Key Operational Considerations for JUKI Pick-and-Place Machines
When operating JUKI pick-and-place machines, users should observe the following essential guidelines:
- Power On: First, adhere to the safety and technical operation specifications of the JUKI equipment, and power on the pick-and-place machine.
- Vacuum Pressure Check: Verify that the vacuum pressure of the machine meets the required specifications, typically around 5.5 bar.
- Servo System Activation: Turn on the machine’s servo system.
- Return to Home Position: Ensure that the x and y axes return to their initial reference positions.
- Adjust Conveyor Width: Based on the width of the PCB, adjust the guide rail width of the drive system, ensuring it is at least 1mm wider than the PCB for smooth sliding.
- Set PCB Positioning Device: Properly set the PCB positioning device to ensure accurate placement.
These operational considerations are fundamental requirements for running JUKI pick-and-place machines. For any issues or inquiries during operation, it is advisable to contact your JUKI machine distributor.
Conclusion
The variety of JUKI pick-and-place machines available today provides SMT companies with the flexibility and efficiency needed to meet diverse production needs. By following the outlined operational guidelines, users can enhance machine performance and ensure high-quality manufacturing outcomes.
At YEETAI, we produce all kinds of feeder to upgrade Juki SMT machines.