IR Thermal Cure Oven: Precision Curing with Infrared Technology
Our IR Thermal Cure Oven is an advanced in-line machine specifically for mid-to-high volume production. It integrates seamlessly with all conformal coating systems, providing an efficient solution for thermal curing processes. This CE-certified oven comes with precise control capabilities for conveyor speed and the internal thermal environment, ensuring optimal curing conditions.
Key Features of the IR Thermal Cure Oven
- Dual Stepper Motors:
- Equipped with dual motors and chains for stable and smooth transmission. This configuration enhances load capacity and supports stepless speed adjustment, ensuring consistent operation.
- Intelligent Temperature Control:
- The IR Thermal Cure Oven features a sophisticated temperature control system with an accuracy of ±2°C. Ou machine can control each thermal zone independently through a PID controller, pulse control, and SSR. Guaranteeing reliable performance throughout the curing process.
- Safety Mechanism:
- The oven incorporates a cylinder lifting mechanism, allowing the upper body to open safely and reliably, enhancing user safety.
- Optimized Internal Structure:
- Design includes a dual outlet turbine system that increases airflow pressure, providing stable wind speed and even temperature distribution. The integrated spiral design utilizes high-quality imported heating wires for rapid thermal exchange, durability, and high heat efficiency. The oven chamber is from stainless steel, ensuring resistance to high temperatures without deformation.
- Durable Guide Rails:
- Constructed with anodized aluminum, the guide rails feature an anti-twist chain for automatic tensioning. Thus this promots longevity and reliability in operation.
- Real-Time Monitoring:
- Each temperature zone features independent sensing sensors. And it allows for continuous real-time monitoring and compensation of temperature balance. Critical for precision curing.
- Adjustable Conveyor Width:
- You can adjust the guide rails in width using a handwheel. So that it allows for versatility in handling various PCB sizes. An emergency stop switch included for added safety.
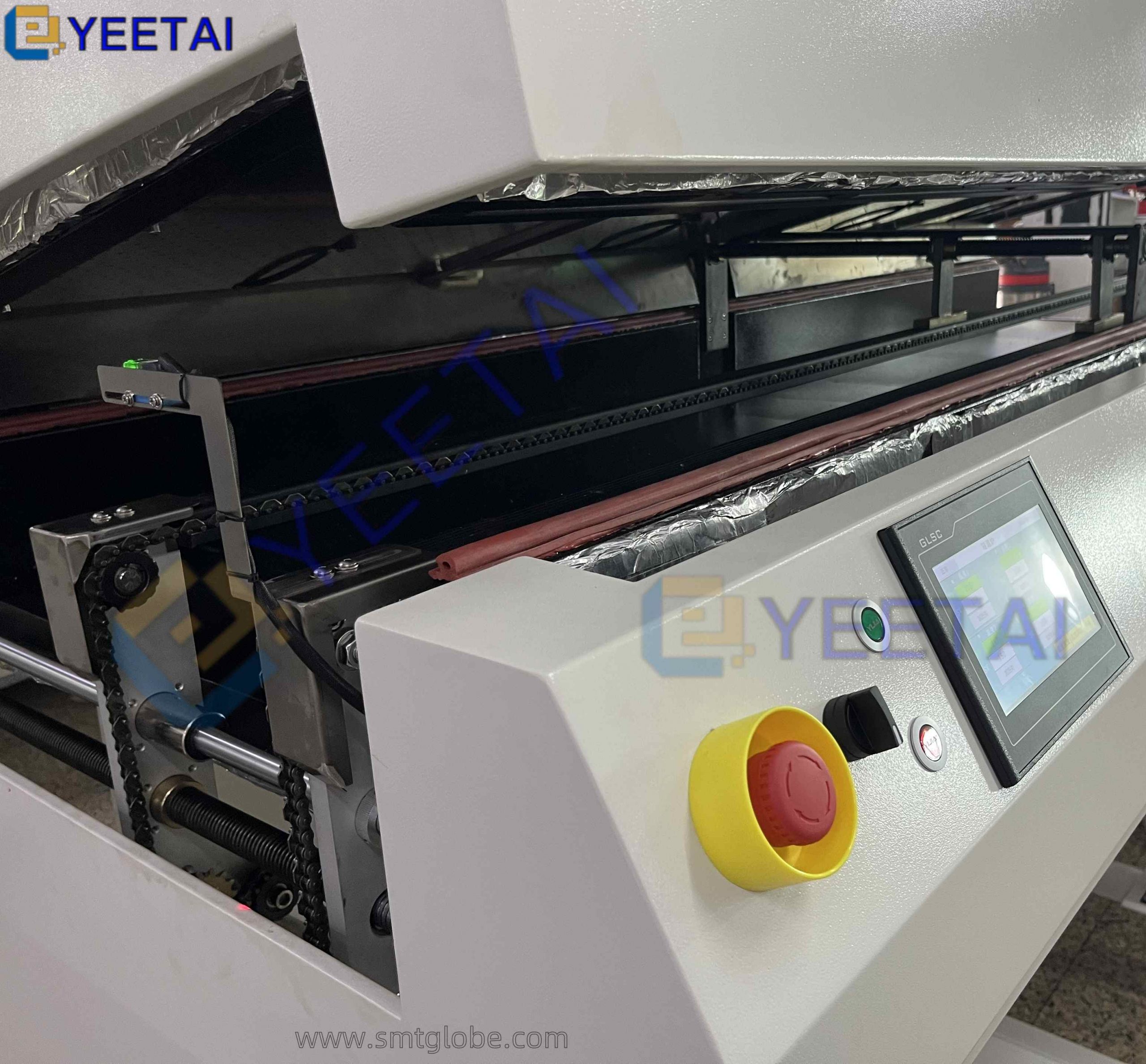
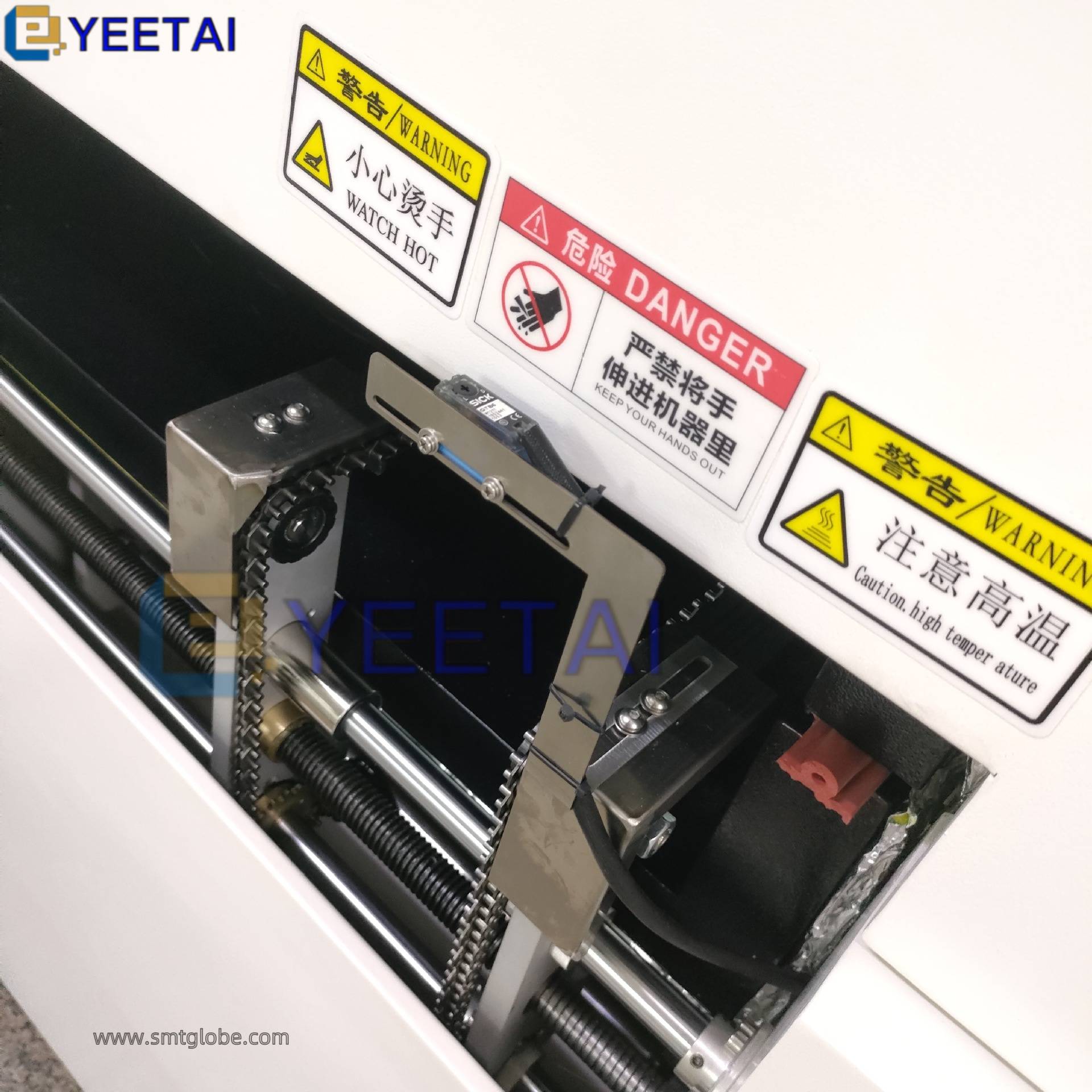
Specifications
No. | Scope of application | |||
1 | Application | Glue dispensing, conformal coating | ||
2 | Max. PCB(MM) | MAX 350(mm) | ||
Machine Body | ||||
1 | Dimension L*W*H(MM) | 2000*1050*1480mm | ||
2 | Heating zone length | 1800mm (3 temperature control zones above) | ||
3 | Weight | 300KG | ||
4 | Temperature zone composition | Upper 3 temperature zones, lower unheated zone | ||
5 | PCB Clearance | 30mm distance between top and bottom | ||
Temperature control | ||||
1 | Temperature control mode | Each temperature zone is independently controlled by temperature control meter PID+Pulse+SSR | ||
2 | Temperature control precision | ±2℃ | ||
4 | Temperature control range | Room temperature~1500C | ||
5 | Temperature rise time (cold machine start) | Around 20 minutes | ||
6 | Temperature stabilization time | Within 2 minutes | ||
Furnace chamber structure | ||||
1 | internal composition | Turbo dual outlets are used to increase the wind speed pressure, resulting in stable wind speed and smooth temperature. | ||
Conveying mechanism | ||||
1 | Conveying method | Guide rail chain transmission | ||
2 | Conveying direction | Left→right, right→left (optional) | ||
3 | Conveyor chain surface height | 900mm±20 | ||
4 | Transportation speed | 0~2200mm/min | ||
5 | Guide rail | Special anti-twist aluminum alloy profile | ||
6 | Chain expansion | Less than 2.5mm | ||
7 | Chain tensioning device | Automatic chain tensioning | ||
Control system | ||||
1 | Power Supply | 3-phase 5-wire 380V | ||
2 | Total power | 12KW | ||
3 | Start-up power/no load power | 10KW/5KW | ||
4 | No-load thermostatic power | Approx. 5KW | ||
6 | Transmission motor | Motor 220VAC single phase 90W | ||
7 | Heater | Spiral 2-position integrated box type, imported high-quality heating wire group, fast heat exchange, long life, high heat utilization rate. | ||
8 | Alarm | Over-temperature alarm, automatically cut off the heating power |
Machine Configuration for Optimal Curing
- High Precision Temperature Control:
- The IR Thermal Cure Oven ensures a high temperature accuracy of ±2°C, providing stable and consistent curing results.
- Enhanced Transport Mechanism:
- Features a 35B long-axis chain that ensures smooth transportation of PCBs without shaking or deformation, crucial for maintaining product integrity during the curing process.
- Synchronized Guide Rail Transmission:
- The design guarantees precise width adjustments and high durability, effectively resisting distortion during operation.
- Manual Lubrication System:
- You can manually control the lubrication system. It allows operators to manage the timing and quantity of lubrication for the transmission chain as needed.
- PID Controlled Heating Zones:
- Each heating zone utilizes PID control for efficient heating, with a typical temperature ramp-up time of 10-15 minutes.
- Temperature Fault Alert System:
- Features an audible and visual alarm system with LED lights, alerting users to any temperature faults, ensuring quick response and maintaining quality
standards.
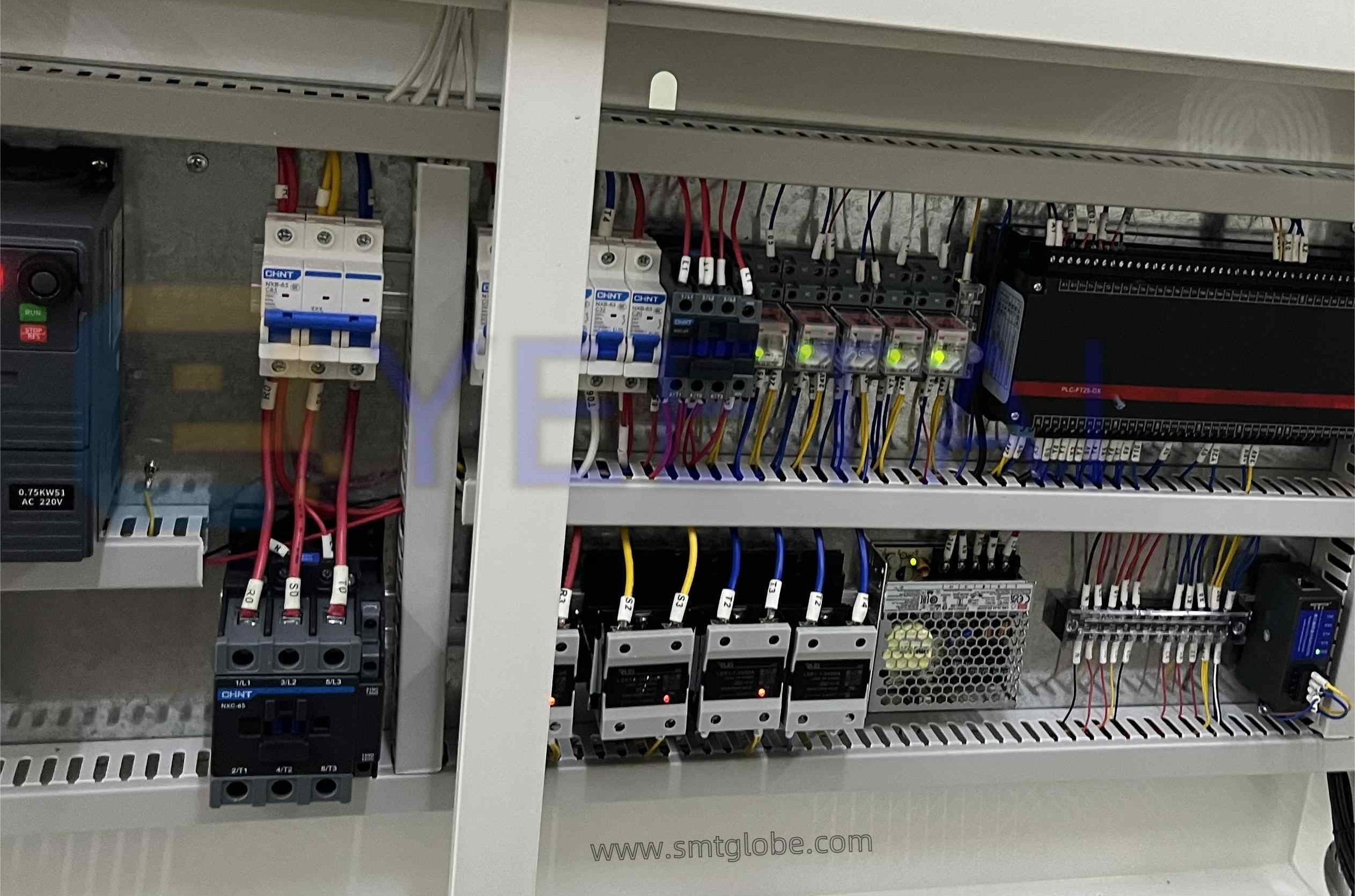
Conclusion
Our IR Thermal Cure Oven stands at the forefront of curing technology, combining infrared ray technology with unparalleled temperature control to achieve superior results. It mains to enhance productivity in high-volume PCB manufacturing while ensuring consistent quality in conformal coating applications.
With its robust features and reliable performance, this oven is an indispensable tool for any modern production environment.
Conformal coating full line solution
We offer full line solutions of conformal coating process. You may read below pages.
Selective Conformal Coating Machine
Full conformal coating machine
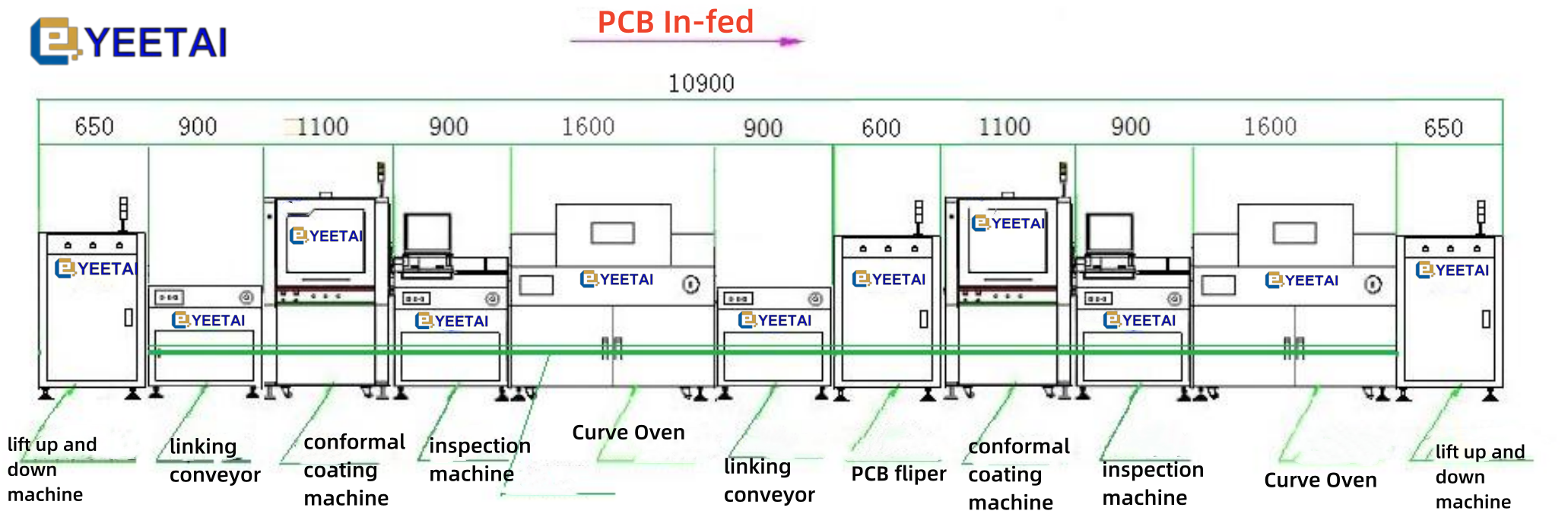