Automated Guided Vehicles (AGVs) are revolutionizing the electronic manufacturing industry, particularly in Surface Mount Technology (SMT) factories. While the benefits of integrating AGVs are significant—enhanced efficiency, reduced labor costs, and improved workflow—ensuring safety during their operation is paramount. This article will discuss essential safety measures that SMT factories should consider when utilizing AGVs in their processes.
1. Conduct Regular Safety Training
One of the most effective ways to ensure safety is through comprehensive training. Workers should be educated on AGV operation, potential hazards, and emergency procedures. Regular training sessions can help staff remain informed about safety protocols and ensure that they understand how to work alongside AGVs without risking accidents.
2. Implement Clear Traffic Management Protocols
Just like in traditional vehicle traffic, establishing clear traffic management protocols for AGVs is crucial. SMT factories should:
- Define AGV Pathways: Clearly mark the pathways that AGVs are allowed to use and ensure that these routes are free of obstacles.
- Signal Systems: Use visual signals, like lights or indicators, to communicate AGV movements. This can alert workers to the presence of an AGV, thereby reducing the risk of collisions.
3. Use Advanced Safety Features
Modern AGVs come equipped with various safety features, including:
- Obstacle Detection Systems: AGVs should be fitted with sensors that allow them to detect obstacles in their path, enabling them to stop or reroute when necessary.
- Emergency Stop Buttons: Each AGV should feature an easily accessible emergency stop button that can be quickly activated in case of an emergency.
- Speed Control: Ensure that AGVs operate within safe speed limits, particularly in areas where workers are present. Speed reduction protocols can minimize the severity of accidents.
4. Regular Maintenance and Inspections
To ensure optimal safety, routine maintenance and inspections of AGVs should be conducted. This includes:
- Routine Checks: Regularly inspect AGV components such as brakes, sensors, and batteries to ensure they are functioning correctly.
- Software Updates: Keep the AGV’s operating system updated to leverage the latest safety features and enhancements.
5. Maintain Clear Communication
Establishing clear lines of communication between operators and factory employees is vital for safety. Consider the following:
- Two-Way Communication Systems: Use two-way radios or intercoms to allow workers to communicate with AGV operators in real-time.
- Safety Meetings: Hold regular safety meetings to discuss any incidents or near-misses involving AGVs and refine safety protocols accordingly.
6. Define Safety Zones
Create designated safety zones within the production environment where workers should not enter while AGVs are operating. By clearly marking these areas and enforcing compliance, you can significantly reduce the risk of accidents.
7. Monitor AGV Activities
Implementing monitoring systems to oversee AGV operations can also enhance safety. Real-time tracking can:
- Identify Patterns: Analyzing AGV movement patterns can help pinpoint potential safety issues before they escalate.
- Ensure Compliance: Monitoring can ensure that AGVs adhere to established pathways and speed limits.
Conclusion
While AGVs present numerous advantages for SMT factories, prioritizing safety is crucial to avoid accidents and injuries. By conducting regular safety training, implementing clear traffic management protocols, utilizing advanced safety features, and fostering open communication, SMT manufacturers can ensure a safe working environment.
By taking these precautions, factories can maximize the benefits of AGV technology while minimizing risks, ultimately leading to a more efficient and safer electronic manufacturing process. Embracing a culture of safety will not only protect employees but also enhance productivity and operational efficiency in the ever-competitive electronic manufacturing landscape.
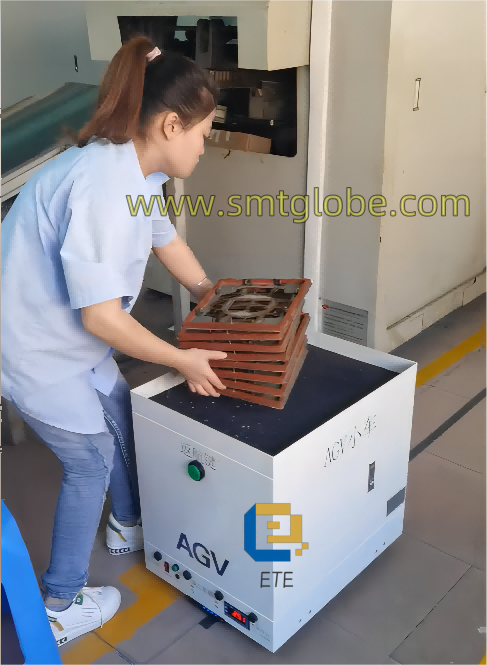
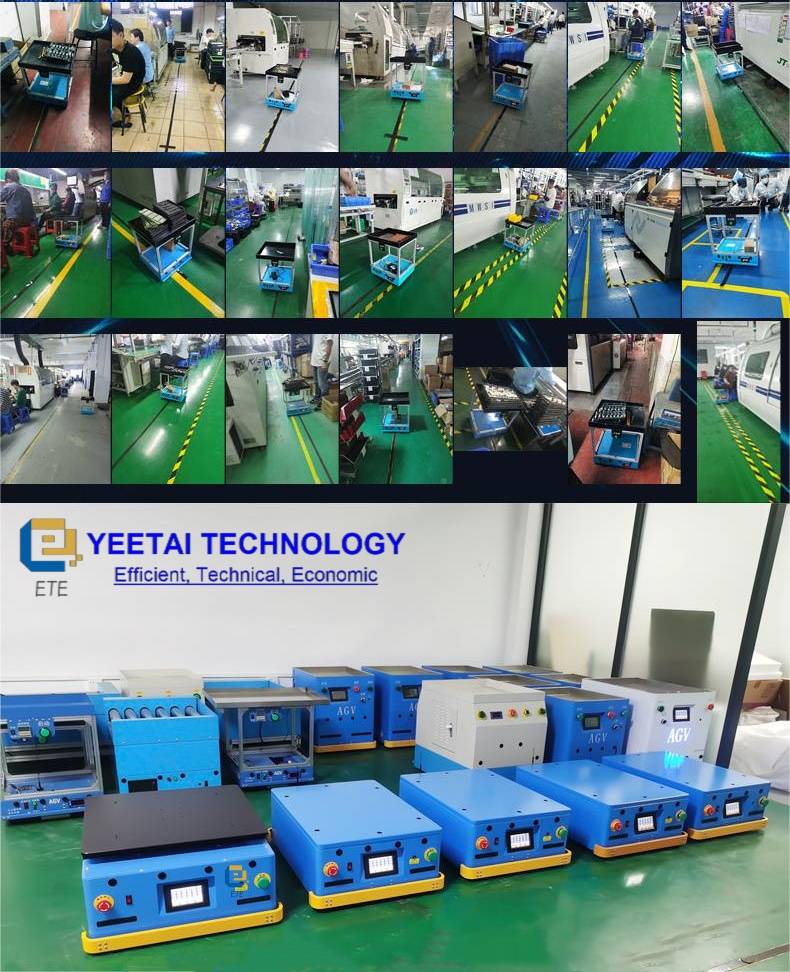
If you need any solutions, we are here to help.
Laser-guided SMT AGV Robot ETE-AGV-910A
SMT AGV Equipment for moving wave soldering pallet | ETE-AGV30-C
SMT Automatic Guided Vehicle ETE-AGV100-T
AGV for PCB moving | ETE-AGV100-L
Wave Soldering Pallet AGV | ETE-AGV60
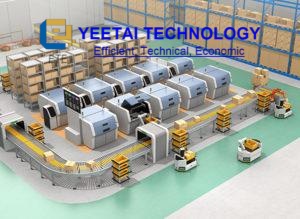