E4420 is an inline axial inserter equipped with a board handling system that enables automatic loading and unloading of PCBs. It can automatically insert components supplied on tape into printed circuit boards (PCBs). This machine features multiple sets of independent servo control systems, ensuring high stability in component insertion performance to achieve optimal speed and density. Its application software is based on the Windows XP system, with a user-friendly interface that facilitates human-machine interaction. The machine enhances component efficiency and PCBA product quality. It primarily offers four key functions: “Component Sequencing,” PCB loading and unloading, “Component Insertion,” and “Component Pin Cutting and Forming.”
Component Sequencing: The module of the axial inserter includes a distribution head used to cut axial components from reels or component boxes and place them on the sorting machine chain. The component sequence is predetermined by the product program. The components are then transferred to the chain at the machine head for delivery to the insertion tool. The program controls the position and direction of component insertion.
Component Insertion: A product program is created with information related to the components, PCB board, and processing requirements. Once this product is called, the operation of the axial inserter can begin.
Component Lead Cutting and Forming: After fully inserting into the PC board, the cutting and clinching unit of the axial inserter will cut and form the component pins (clinching) to mechanically secure them to the board. This process continues until the product is completed, and all required axial components are in place. When the program is finished, the PCB is removed from the machine or transferred.
PCB Loading and Unloading: The axial inserter can load the PCB onto the machine’s working table. Once the insertion task is completed, the board handling system will unload the PCBA from the machine to the adjacent machine. PCBs can flow from left to right or from right to left. The available automatic board handling type is the Board Handling System (BHS) for L-to-R or R-to-L board transfer. Automatic board handling enables continuous machine operation by loading and unloading PCBs without the need for operator intervention. It is best suited for high-volume applications with low-to-medium job changeovers.
The Component Sequencer and feeder function involves modules of the axial insertion machine that include a distribution head for cutting horizontal components from reels or trays and placing them on the sorting machine chain. The sequence of components is predetermined by the product program. The components are then transferred to the VCD head chain for delivery to the insertion tool, with the program controlling the position and direction of component insertion.
For Component Insertion, a product program is created with information related to the components, PCB board, and processing requirements. Once this product is called upon, the operation of the axial insertion machine can begin.
After fully inserting into the PC board, the cutting and clinching unit of the axial insertion machine cuts and forms the component pins mechanically (clinching) to secure them to the board. This process continues until the product is completed, and all required horizontal components are in place. When the program is finished, the PCB is either removed from the machine or transferred.
Specification
Machine model | E4420 |
Theoretical speed | 24,000 components/hour |
Insertion direction | Parallel 0 degrees, 90 degrees, 180 degrees, 270 degrees |
Lead Span | Double hole spacing 5-20mm |
Substrate Size | Minimum 50*50mm; Maximum 320*400mm |
Substrate Thickness | 0.79-2.36mm |
Component Type | Capacitors, transistors, diodes, resistors, fusible wires, etc. Braided tape encapsulation material |
Jumper | Independent conveying method. Diameter 0.5mm-0.8mm tinned copper wire |
Component Lead Cutout Length | 1.2mm-2.2mm (adjustable) |
Component Lead Angle | 5-35 degrees (adjustable) |
Machine Dimension (L*W*H) | Main machine 1700mm*1500mm*1800mm ; feeding station 1200mm*1000mm*1410mm(20 stations) |
Machine Weight | Weight of main machine 1200KG;Weight of sub-machine 800KG |
Power Supply/Power Used | 220V,Ac(single-phase)50/60Hz,1.5KVA/1.6Kw(energy-saving type) |
System protection | Built-in ( USP) power failure protection power supply |
Use of air pressure (air consumption) | 0.4-0.6Mpa/0.3 cubic meters/minute(dry gas) |
Ambient Temperature | 5-25 degrees |
Machine noise | 65dB |
Hole correction method | Machine vision system, multi-point MARK vision correction |
Drive system | AC servo, AC motor |
Data input method | USB interface input (EXCEL file format) |
Control system | Chinese operation interface (WINDOWS XP system control platform) LCD monitor |
Table operation method | Clockwise and counterclockwise |
PCB loading method | Automatic, from left to right or right to left |
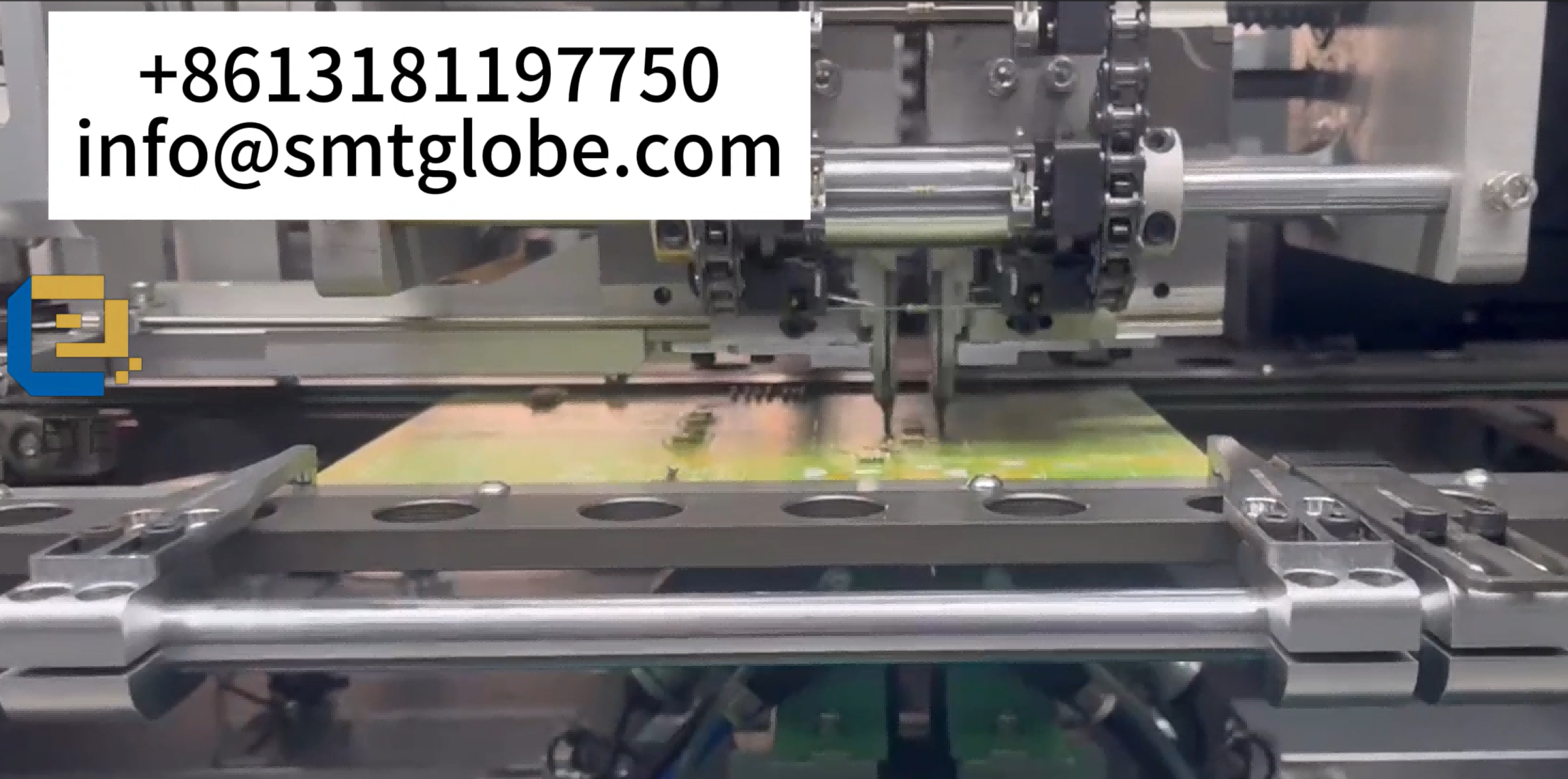
Features:
E4420 provides you with an efficient and stable solution for the best axial component insertion, ensuring that all requirements of your through-hole insertion process are met.
With an optional new freely rotating platform, the E4420 axial inserter can easily achieve the process requirements of inserting components at any angle up to 360 degrees, significantly reducing process bottlenecks and manual intervention.
The stress caused by the mechanical motion of component pin forming tools can have a certain impact on the internal structure of the components. The E4420 axial inserter adopts a 45-degree V-shaped forming tool, which significantly improves tool cutting resistance, keeping tensile interference within a minimal range to ensure process reliability.
The new generation intelligent feeder is more compact and efficient. The newly developed intelligent modular feeder occupies a smaller footprint but still achieves a super high-speed capacity of 24,000 CPH. It effortlessly achieves high-efficiency production under the most stringent area conditions. You can also expand up to 80 stations to meet future process requirements.
The Axial inserter boasts proprietary tooling with a high-efficiency and stable feeding drive structure. It offers expandable and precise sequencing capabilities along with component feeding that ensures zero jumper lead scrap. With its flexibility and precision, the machine can insert a full array of axial lead components and jumper wire diameters in a single operation.
The axial inserter features an Automatic board handling system that enables uninterrupted machine operation through the automated loading and unloading of PCBs, eliminating the need for operator involvement. This system is particularly well-suited for high-volume production scenarios with minimal to moderate job changeovers. The axial inserter is SMEMA compatible.
Setting an industry benchmark, it achieves the highest real throughput of 24,000 components per hour (CPH) and boasts world-class reliability at 300 parts per million (ppm). The programmable clinch height feature of the Axial inserter safeguards against damaging surface-mount device (SMD) components, while also verifying component value and polarity before insertion.
Enhanced by a Rotary Table, the machine is equipped with long-life tooling and low-profile locators that reduce wear and extend operational lifespan. Its low maintenance requirements and user-friendly programming interface, facilitated by a USB port for data transfer and support for Gerber format (Excel) file input, ensure efficient and swift operations.
Moreover, the machine is equipped with built-in power failure protection (USP) and allows for component replenishment without halting operations. It also features a dual-part detector that can sense two parts on the chain simultaneously, enhancing operational efficiency and reliability.
Advantages of the Axial insertion machine:
- Replaces manual labor with automated operations.
- Achieves a theoretical speed of 24,000 components per hour.
- Offers simple operation and high stability for consistent performance.
- Enables flexible production deployment with versatile capabilities.
- Features low maintenance costs, ensuring cost-effective operation.
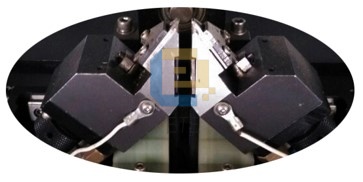