Automatic insertion machines are pivotal in the assembly of electronic components, and their efficiency and reliability largely depend on the condition of critical parts, particularly the blades. Regular checks and maintenance of these blades are essential to ensure optimal performance and safety.Contact us to know how to have checks for your machines. Here are some key practices to follow:
Importance of Blade Selection and Maintenance
The blade is one of the most critical components of an automatic insertion machine. Proper selection and maintenance of the blade are vital for operational safety and efficiency. A high-quality blade not only improves performance but also reduces potential safety hazards.
Blade Selection
- Sound Quality Check: A good blade should produce a clear sound when struck. To test this, carefully suspend the blade and gently tap it with a wooden mallet while listening closely. If the blade emits a dull sound, it may indicate internal damage or cracks, suggesting that it should not be purchased.
- Avoid Marking: Never use electric engravers or sharp objects to mark the blade, as this can damage its integrity. Proper care during handling is essential.
Blade Handling and Storage
- Safety Precautions: The blade’s edge is extremely sharp and can pose a risk to operators. Avoid contact with skin or other hard materials to prevent accidents.
- Proper Storage: Spare blades should be stored in designated areas and handled by trained personnel. Improper storage can lead to damage or accidents.
- Installation: Before installing a new blade, ensure that the mounting surface of the machine is clean and free from dust, debris, and cutting residue. This helps maintain the machine’s efficiency.
Blade Installation Steps
- Align the Blade: Carefully place the blade on the mounting surface of the machine. Rotate the machine’s bearing to align the blade with the center.
- Attach the Blade Holder: Position the blade holder over the blade, ensuring the bolt holes align with those on the machine’s bearing.
- Secure the Blade: Insert the hexagonal screws and tighten them using an appropriate tool to secure the blade firmly.
- Self-Check: After installation, ensure there is no looseness or misalignment. Although everything may seem fine, safety measures must be in place to prevent unexpected incidents. Operate the machine at a speed limited to 4,500 RPM to avoid accidents.
Pre-Operational Checks
Before starting operations, conduct a trial run to verify that the machine functions correctly. During the drilling process, advance the PCB at a steady pace, avoiding rapid movements that could cause damage to the blade or lead to serious accidents.
Blade Storage
When not in use, blades should be kept clean and free from contaminants. The cutting edge should be covered with a PVC rubber tube and secured with packing tape to prevent damage.
Conclusion
Implementing these checks and maintenance practices can significantly enhance the productivity and quality of operations involving automatic insertion machines. A well-maintained blade is crucial, as the overall economic efficiency of the machine relies heavily on the quality of its blades. By prioritizing blade selection and maintenance, operators can ensure the safe and effective functioning of automatic insertion machines.
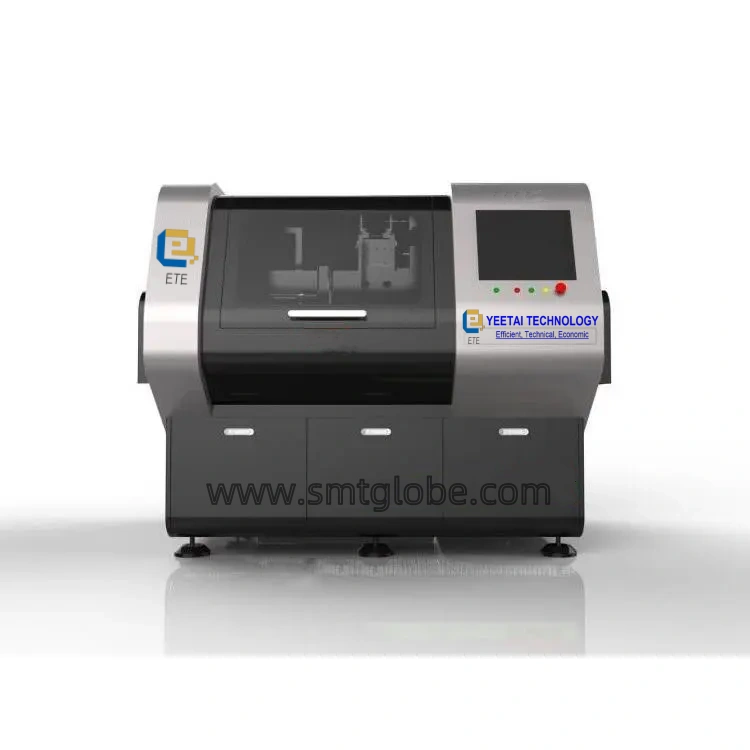
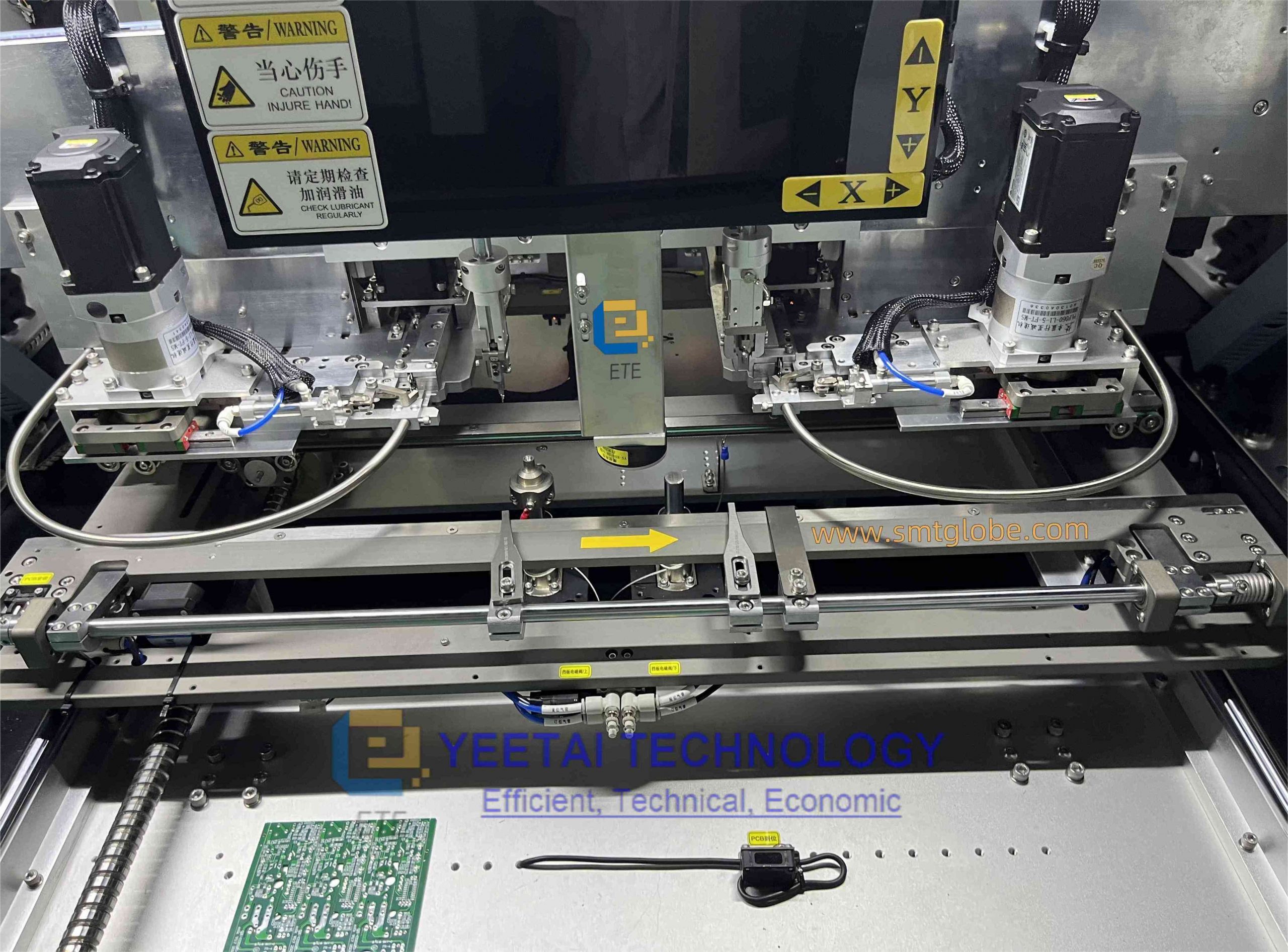
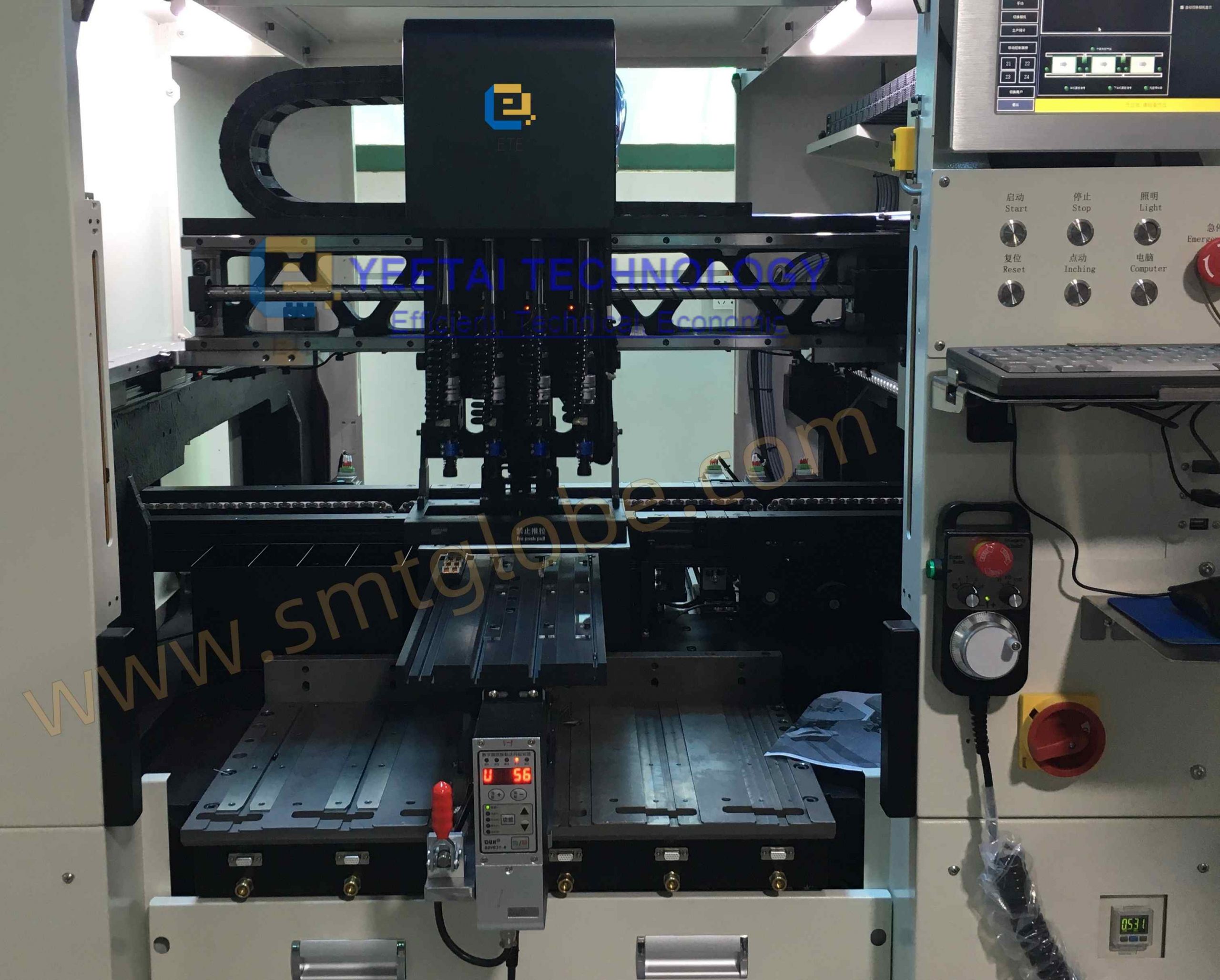
5. Increased Processing Speed
Incorporating high-performance, fast-processing integrated circuits can significantly improve the efficiency of automatic insertion machines. Reducing the number of electronic components can lower the risk of failure points within the system. This not only enhances reliability but also shortens development cycles, making the machines more efficient.
By implementing these strategies, automatic insertion machines can reduce defect rates, minimize production costs, increase operational efficiency, and limit the risks associated with operator errors. These benefits are vital as the industry evolves and the demand for automation grows. As technology continues to advance, it is crucial for manufacturers to consider these improvements to remain competitive in the ever-evolving market of electronic assembly.
We can help to simplify and qualify your PTH PCB assembly process.