Automated Guided Vehicles (AGVs) play a vital role in modern automated manufacturing and logistics systems. The structure of SMT Automated Guided Vehicles is composed of several key components, including the chassis, frame, shell, control room, gearbox, motor, and wheels. This article explores the essential structural elements that make up an AGV and their specific functionalities.Knowing about AGVs Structure ensures that SMT factories could have a better maintenance when utilizing AGVs in their processes.You may know how to manufacture an AGV robot through this article.
1. Chassis and Outer Shell
The chassis serves as the foundation of the SMT AGV, integrating all mechanical and electrical structures necessary for its operation. It features design characteristics typical of electric vehicles while also incorporating unique requirements for autonomous operation. Constructed primarily from welded steel components, the lower the center of gravity, the more stable the vehicle becomes. Essential equipment such as the mobile devices, electrical control systems, buttons, and displays are generally mounted on a dedicated panel.
2. Frame Structure
The frame is integral to the SMT AGV’s overall structure, primarily designed to support wheels, photo sensors, servo motors, and gear reducers. The servo motor driver, PCD board, and batteries are mounted on this frame. The design must meet adequate strength and rigidity standards, typically using cast aluminum alloys, though specifications can be customized to meet client requirements.
3. Wheels
The AGV utilizes solid rubber tires for its wheels, enhancing durability and performance. The two rear drive wheels, fixed and connected to hub motors, provide traction and power. In contrast, the front two wheels are swivel wheels, which facilitate maneuverability and balance, supporting the overall stability of the vehicle.
4. Load Transfer Mechanism
The load transfer system consists of a flat platform designed to transport box components to designated stations. This mechanism is mainly used for loading box components and transporting materials efficiently throughout the operational environment.
5. Drive System
The drive system is the subsystem responsible for the operation of the SMT AGV. It includes capabilities for speed control and braking. Major components of the drive system consist of the motor, gearbox, driver, controller, and driving circuits. The drive system generally operates in two modes: closed-loop, primarily using servo DC motors, and open-loop, mainly utilizing stepper motors.
6. Power System
The power system is the sole power source for the AGV, providing energy to drive the vehicle and support auxiliary systems, including control, communication, and safety protocols. Surrounding facilities utilize standard industrial power, depending on the specific application requirements. Examples include charging rooms, frequency generators, automatic doors, computer rooms, and communication devices. Various power levels are used according to the vehicle type, operational demands, and load capacity, with common DC voltages including 12V, 24V, 48V, and 72V.
Conclusion
Understanding the structure of SMT Automated Guided Vehicles is essential for optimizing their operation and maintenance. Each component plays a critical role in ensuring efficient, autonomous transportation of materials within industrial settings. By leveraging these sophisticated designs, businesses can enhance productivity and streamline their logistics processes.
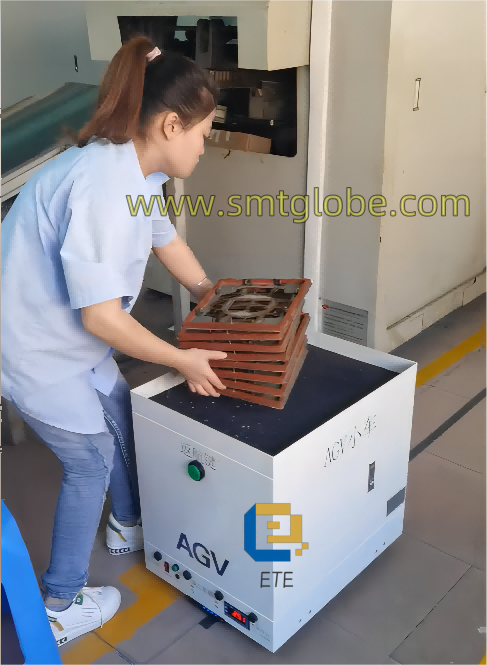
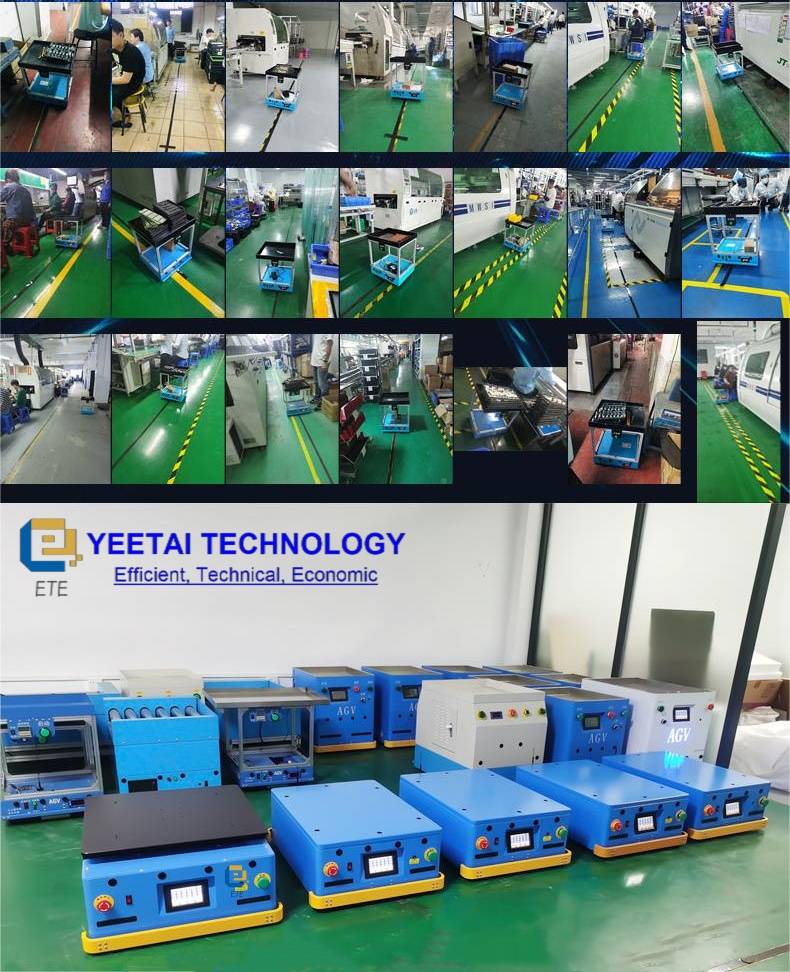
If you need any solutions, we are here to help.
Laser-guided SMT AGV Robot ETE-AGV-910A
SMT AGV Equipment for moving wave soldering pallet | ETE-AGV30-C
SMT Automatic Guided Vehicle ETE-AGV100-T
AGV for PCB moving | ETE-AGV100-L
Wave Soldering Pallet AGV | ETE-AGV60
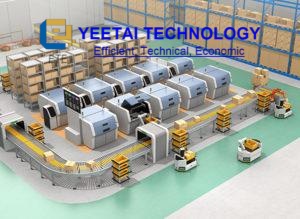