Automated Guided Vehicles (AGVs) are integral to flexible manufacturing systems and automated warehousing, serving as core devices for linking and orchestrating continuous material operations. With the ability to autonomously navigate pre-set routes, AGVs transport goods or materials from their starting point to the designated destination, facilitating automatic transportation of raw materials and components throughout the production process, seamlessly integrating production lines, and managing finished goods entry into warehouses. Below, we discuss the advantages of AGV robots and three key application solutions. You can know what AGV can do for your production.
Advantages of AGV Robots
- Enhanced Automation Levels
Implementing AGV robots significantly improves the automation of material handling, loading and unloading of workpieces, and machine assembly processes. This increase in automation leads to enhanced labor productivity, reduced production costs, and a faster transition toward mechanization and automation in industrial production. - Improved Working Conditions and Safety
AGVs can safely perform hazardous tasks in challenging environments, thereby improving labor conditions for workers. Simple but tedious handling tasks can be efficiently replaced by AGV robots, minimizing the risks associated with human fatigue or negligence. - Reduction of Labor Costs and Rhythmic Production
By replacing human labor with AGVs, businesses can significantly save on labor costs. AGVs can operate continuously, 24/7, without fatigue or the need for salaries, allowing for more precise control over production rhythms and fostering a smooth manufacturing process. - Space Efficiency
Intelligent manufacturing facilities utilizing AGVs and automated assembly lines optimize space usage, leading to more compact factory layouts and lower land resource costs. - Simplified Oversight
In traditional manufacturing settings, despite numerous regulations, monitoring employee productivity can be challenging. The integration of AGV robots reduces the number of human workers, streamlining management and enhancing efficiency. - Flexible Production Lines
AGV robots are highly flexible; they can transition from one task to another seamlessly. Multiple AGVs can form mobile assembly or processing stations, contributing to the establishment of highly adaptable production lines.
Three Key Application Solutions for AGV Robots
- Automated Warehouse Management
AGVs are extensively used in warehouses for the automated handling of inventory. They can efficiently transport materials from storage to picking areas, improving overall warehouse efficiency and significantly reducing human error. - Manufacturing and Assembly Line Support
AGV robots facilitate efficient movement of assembled parts and components between stations on a production line. Their flexibility allows manufacturers to adjust operations quickly, meeting varying production demands without significant delays. - Distribution and Logistics
In the logistics sector, AGV robots streamline the movement of goods from distribution centers to loading docks. They can operate continuously, ensuring timely deliveries and enhancing overall logistics efficiency.
Conclusion
The incorporation of AGV robots offers numerous advantages, including increased automation, improved safety, reduced labor costs, enhanced space efficiency, simplified management, and greater production flexibility. Their diverse application solutions in warehouse management, manufacturing support, and logistics demonstrate AGVs’ critical role in transforming modern industrial operations. As industries continue to evolve, AGV technology will undoubtedly remain at the forefront of innovation in operational efficiency and productivity.
Three Key Application Solutions for AGV Robots in Manufacturing
Automated Guided Vehicles (AGVs) have become indispensable in the manufacturing sector due to their myriad advantages. As industries seek to enhance efficiency and minimize human exposure to hazardous environments, AGV robots have emerged as versatile solutions. Below are three primary application scenarios where AGV robots are transforming operations.
1. Conversion of Tools and Collaborative Mechanisms for Disinfection
In response to growing sanitation requirements, particularly in hospitals and public spaces, AGVs can be modified to function as disinfection robots. This application integrates existing disinfection equipment with an AGV platform, allowing it to autonomously navigate high-risk areas. By employing the AGV’s control system, the robot performs disinfection tasks without direct human intervention, thereby significantly reducing the risk of infection. This innovative solution not only addresses immediate health concerns but also sets a precedent for future robotic applications in safety and sanitation.
2. Automated Transport of Material Carts with Access Control Integration
Another effective application of AGV robots involves the automated handling of material carts. This solution incorporates a lifting and rotating mechanism that identifies the position of a material cart’s legs, allowing the AGV to align itself accurately. Once in position, the AGV can lift the cart for movement, streamlining logistics in confined spaces. Additionally, this system includes communication capabilities with access control systems. This means that AGVs can interact seamlessly with elevators and automatic doors. When a door recognizes the AGV, it grants access, enabling the robot to transport materials efficiently across different floors, effectively solving the longstanding challenge of vertical logistics in manufacturing environments.
3. Automated Pallet Handling with Intelligent Charging Solutions
AGVs equipped with lifting and rotating mechanisms gain the ability to handle pallets as well as material carts, providing a dual-use feature that meets diverse material transport needs within facilities. This versatility not only simplifies logistics but also reduces the variety of robotic types needed, which lowers maintenance costs. Moreover, these AGVs can automatically recharge, ensuring continuous operation around the clock. With customizable low battery and idle-time charging thresholds, manufacturers can adapt the AGV’s charging schedule to fit their operational demands, thereby maximizing efficiency and uptime.
Conclusion
AGV robots are revolutionizing manufacturing logistics through innovative applications that address specific operational challenges. From disinfecting high-risk areas to facilitating automated transport and intelligent charging, these solutions enhance efficiency while reducing the risk to human workers. As manufacturing continues to evolve, the integration of AGV technology stands as a testament to the industry’s commitment to innovation and safety. By adopting AGV robots, manufacturers can not only improve their workflows but also prepare themselves for the future of automated operations.
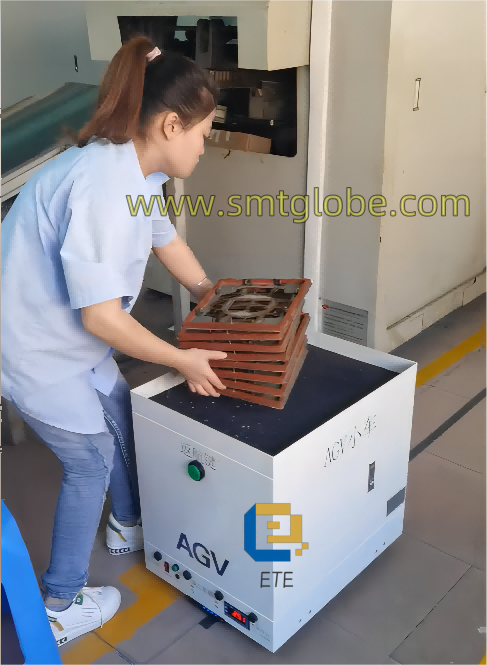
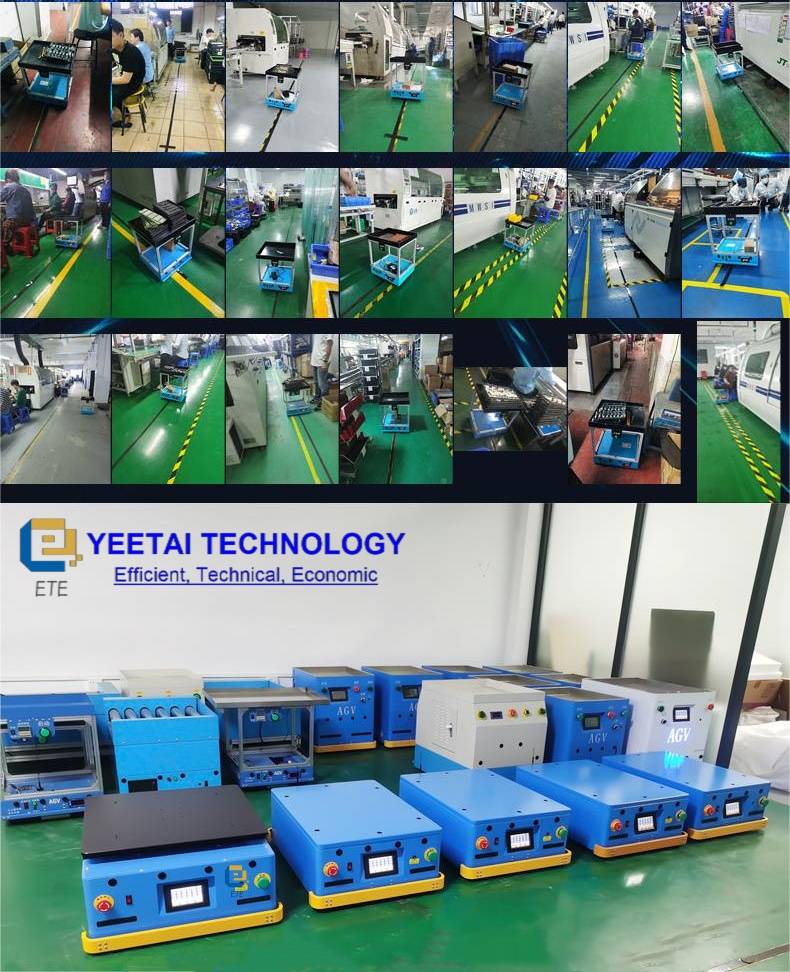
If you need any solutions, we are here to help.
Laser-guided SMT AGV Robot ETE-AGV-910A
SMT AGV Equipment for moving wave soldering pallet | ETE-AGV30-C
SMT Automatic Guided Vehicle ETE-AGV100-T
AGV for PCB moving | ETE-AGV100-L
Wave Soldering Pallet AGV | ETE-AGV60
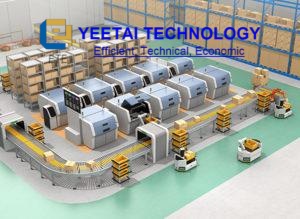