Advanced AGV Wireless Charging Station
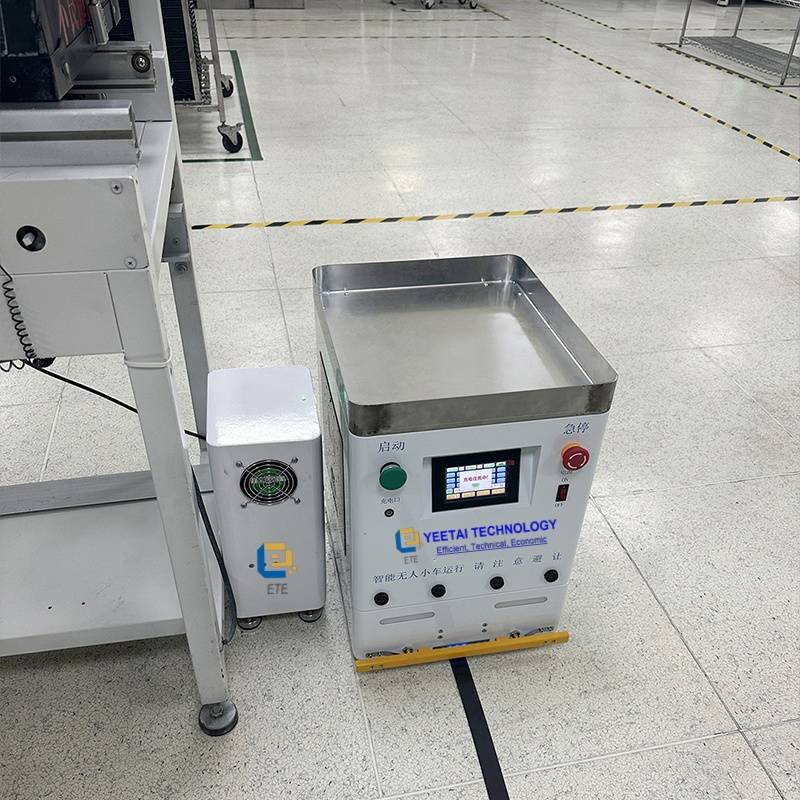
The ETE-AGVC-820 is a state-of-the-art wireless charging station tailored for SMT AGV Robots, offering a simple, lightweight, low-power, and long-endurance automatic charging solution. Its advanced technology includes electromagnetic induction non-contact charging, adaptive control to overcome charging distance and load variations, and a range of safety features for reliable battery protection and longevity.
AGV Wireless Charging Station Feature
- Adaptive control technology effectively addresses challenges related to varying charging distances and fluctuating loads, guaranteeing robust battery protection mechanisms and significantly prolonging battery lifespan.
- Our cutting-edge solution seamlessly integrates with all AGV car models, offering a high degree of customization to meet specific requirements.
- Embracing contactless charging technology, our system prioritizes safety and reliability, ensuring a seamless and secure charging process.
- AGV Wireless Charging Station with depleted battery levels benefit from automatic recharging functionality, eliminating downtime and maximizing operational efficiency.
- Enjoy the convenience of wireless battery replenishment, enabling hassle-free and efficient power management for your AGVs.
- Our system is equipped with comprehensive protection features, including safeguards against short circuits, leaks, and overcurrent situations, ensuring the safety and longevity of your batteries.
- To maintain optimal operating temperatures, our solution includes a high-speed fan for effective cooling, enhancing the overall performance and reliability of the system.
Specification
Model ETE-AGVC-820 charging method Electromagnetic induction non-contact charging (launch plate and contact plate cooperate) Input voltage AC220V take over 25.2V 5A Charging voltage P 25.2V recharging current 2-5A Data transmission frequency band 2.400-2.485GHz 2.4G wireless communication pairing Voltage regulation accuracy ±5% Steady current accuracy ±5% voltage ripple W5% Self-weight of charging pile 5.65KG Launch disc size (MM) Length 130X Width 130X Height 130 (customizable) Receiving host size (MM) Length 280X Width 280X Height 280 (can be customized) cooling high speed fan Working temperature -20~+40 Charging distance 10~30mm level deviation ±20mm Electric pile size (MM) Length 170X Width 220X Height 385 Suitable for AGV models All AGV robot models (customizable)
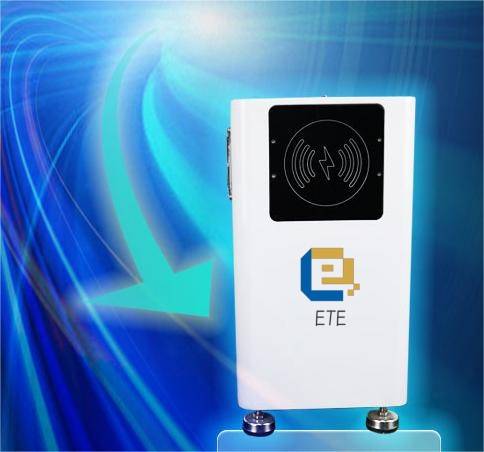
Working method: It Utilizing wireless charging technology, energy transfer is achieved through electromagnetic induction between AGV vehicles and charging stations. Within the working area, charging stations are equipped with wireless charging facilities, while corresponding receivers are installed on AGV vehicles. When an AGV vehicle approaches a charging station, the wireless charging facility transmits electrical energy to the vehicle, allowing it to receive power and charge while in operation.
Wireless charging eliminates the need to connect to charging stations, as it utilizes the built-in wireless charging device within AGV robots for recharging. The wireless charging device converts electrical energy into a magnetic field and transfers this field to the battery pack of the AGV robot, enabling the charging process. The advantage of wireless charging is its convenience and simplicity, allowing for charging anytime and anywhere, making it suitable for AGV robots that require frequent movement.
Whether using wired or wireless charging, it is crucial to prioritize charging safety. During charging, precautions should be taken to prevent AGV robots from coming into contact with live electrical components and to avoid issues such as power overloads. Additionally, regular inspection and maintenance of the battery pack of AGV robots are necessary to ensure longevity and performance.
In conclusion, there are various charging methods available for AGV robots. By selecting the appropriate charging method based on specific requirements and emphasizing charging safety, the lifespan and performance of AGV robots can be maintained, contributing to the stable and efficient operation of automated production lines.