We tailor a AGV robot to streamline wave soldering production line for an SMT factory in the electronic industry. What is an AGV robot and how it works for wave soldering pallet return?
To understand the working principle of AGV (Automatic Guided Vehicle) robot, firstly we need to understand its definition, which is: AGV (Automatic Guided Vehicle), also known as unmanned handling vehicle, automatic vehicle, or handling robot. It refers to a transport vehicle equipped with automatic guiding devices such as electromagnetic or optical, radar, and laser, which can travel along a specified guiding path, with safety protection and various handling functions. Its main features include car programming, parking selection device, safety protection, and various handling functions, and it can autonomously drive without human intervention under the supervision of a computer, automatically travel along a specified guiding path, reach the designated location, and complete a series of tasks. Its system technology and products have become important equipment and technology for flexible production lines, flexible assembly lines, and warehouse logistics automation systems.
When it receives a material handling instruction, the controller system calculates, plans, and analyzes the best route based on the stored operating map and the current position and direction of the AGV robot, automatically controls the driving and steering of the AGV robot, and when the AGV reaches the loading position and accurately stops, the handling mechanism acts to complete the loading process. The AGV then starts and drives to the unloading point, stops accurately, and the handling mechanism acts to complete the unloading process, and reports its position and status to the control system. The AGV then starts and drives to the standby area and waits for the next handling instruction.
AGV Robot structure composition: The basic structure of the AGV robot consists of three main systems: mechanical system, power system, and control system. The mechanical system includes the body, wheels, steering device, handling device, and safety device, while the power system includes the battery and charging device, drive system, safety system, control and communication system, and guiding system.
(1) Body
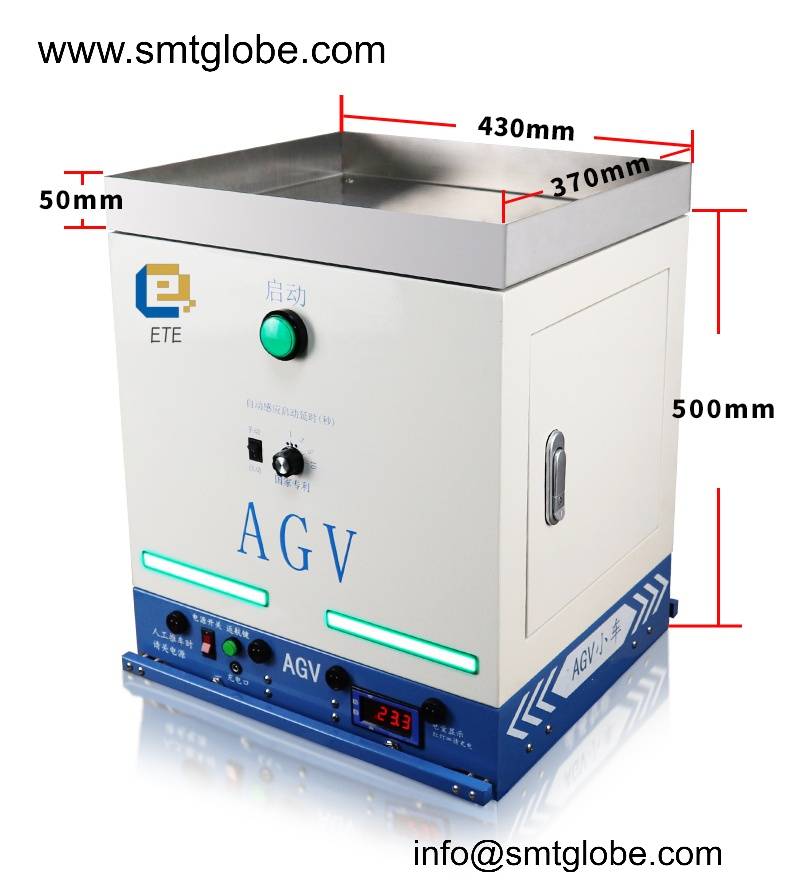
The body of the AGV robot mainly includes the chassis, drive mechanism, and steering mechanism, serving as the foundation for the installation of other components.
The drive mechanism consists of the driving wheel, gearbox, brake, drive motor, and speed controller (governor), forming a servo-driven speed control system.
Depending on the AGV’s operating mode, common steering mechanisms for AGVs include pivot steering, differential steering, and all-wheel steering. Through the steering mechanism, the AGV can drive in a complex movement, including forward, backward, longitudinal, lateral, diagonal, and rotational motion.
The power unit of the AGV robot generally consists of a rechargeable battery and its charging and discharging control device. The battery is an industrial battery with a voltage of 24V or 48V, available in options such as lead-acid, nickel-cadmium, nickel-zinc, nickel-metal hydride, and lithium-ion batteries. In addition to considering factors such as power, capacity (Ah), power-to-weight ratio, and volume, the most critical considerations include the duration of the charging time and ease of maintenance.
Fast charging involves high-current charging and typically requires specialized charging equipment. The AGV itself must have charging limit and safety protection devices.
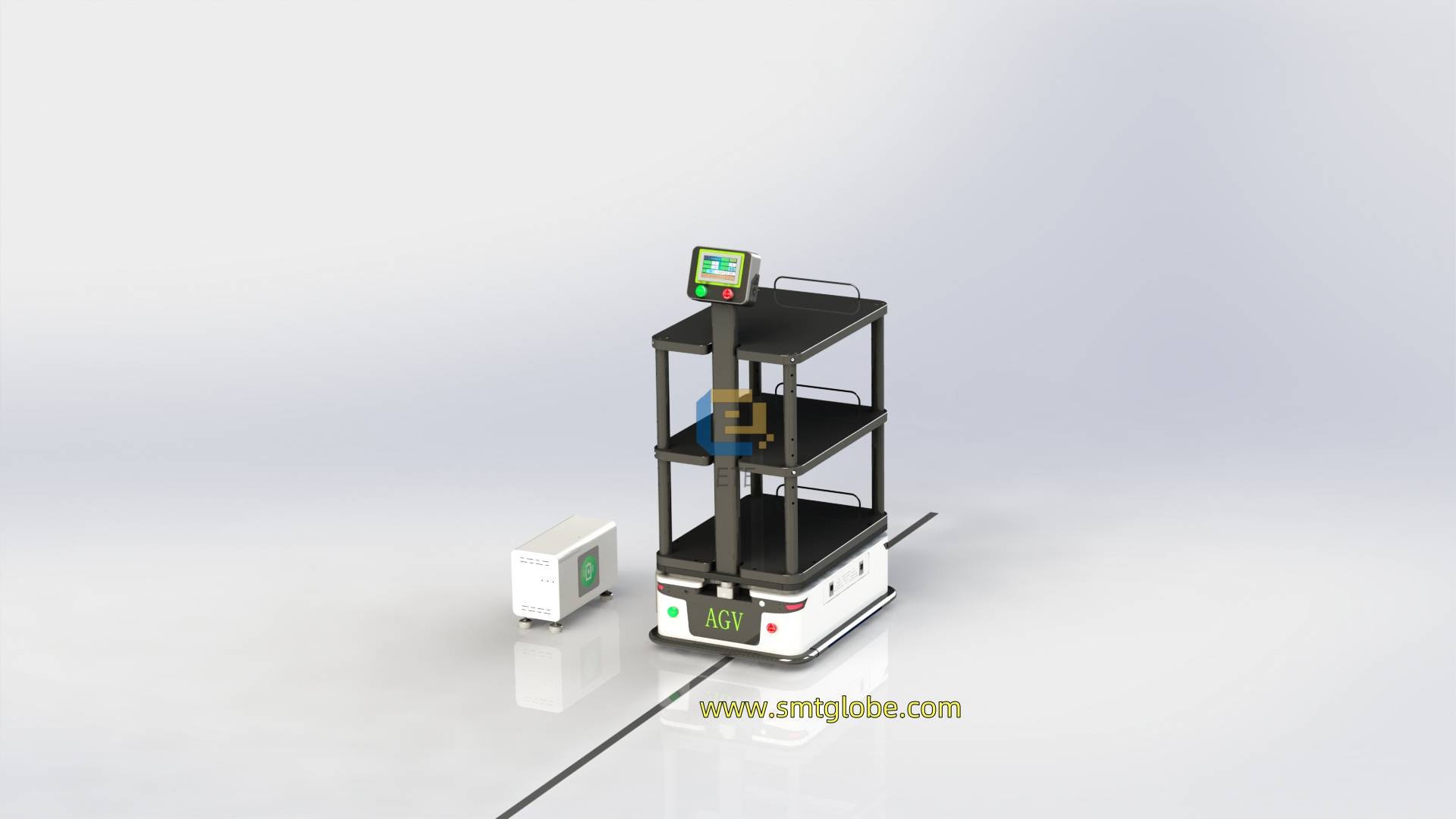
There are automatic chargers att the charging locations along the AGV’s operating route.A charging connector on its underside, which connects to the charging contact plates on the ground when the AGV reaches the charging position, allowing for a maximum charging current of up to 200 amps.
(3)Control system
The control system of the AGV car typically consists of an onboard controller and a ground (external) controller, both of which are currently using microcomputers connected through a communication system.
The onboard controller is responsible for manual control of the AGV, initiating safety devices, monitoring the battery status, steering limits, releasing the brakes, controlling the driving and steering motors, monitoring the charging contactor, and ensuring safe operation.
The ground controller manages AGV scheduling, issues control commands, and receives information about the AGV’s operating status. The control system is the core of the AGV, responsible for the AGV’s operation, monitoring, and implementation of various intelligent controls.
(4) Safety device
Safety measures for the AGV car are crucial to ensure the AGV’s own safety during operation, as well as the safety of personnel and various equipment on-site. Typically, AGVs employ multiple levels of hardware and software safety monitoring measures. This includes non-contact and contact collision sensors at the front of the AGV, prominent signal lights and audible alarms on the top of the AGV to alert nearby operators. In case of a malfunction, the AGV automatically triggers sound and light alarms and notifies the AGV monitoring system using wireless communication.
(5) Guidance system
The guidance system provides directional information to the AGV, enabling it to perform actions such as forward movement, reverse movement, branching, and exiting based on the guidance.
(6) Information transmission and processing system
The information transmission and processing system handles communication and data processing for the AGV.
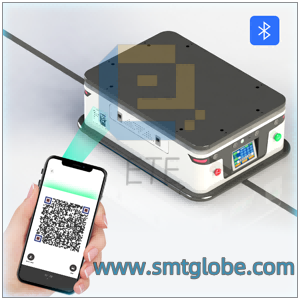
To monitor the AGV, monitor the ground status of the AGV, and communicate real-time information with the ground control station.
(8) Carrying Device
We can also equip the AGV with a carrying device such as rollers, towing bars, and other mechanisms as needed for loading, unloading, and transporting goods.See below picture to learn how our AGV optimizes production line for a SMT factory in the electronic industry. Welcome to contact info@smtglobe.com

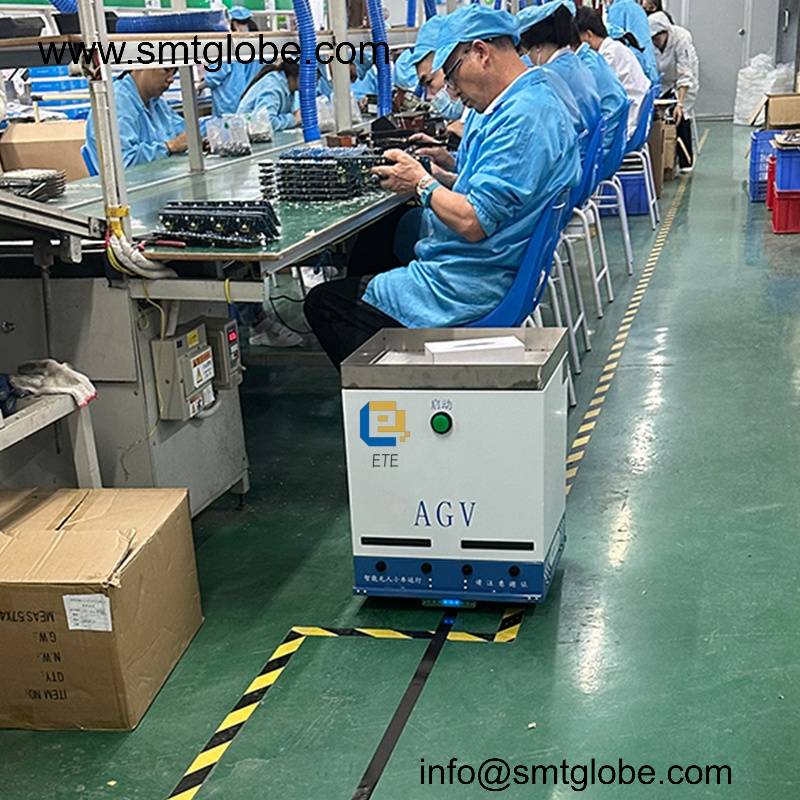