Our AGV for PCB moving is suitable for transporting wave soldering pallets and PCB fixtures in electronic manufacturing. This innovative solution automates processes for electronic manufacturers, streamlining SMT material handling, warehouse logistics, and production lines. With self-guided driving and advanced lithium battery technology, our AGV robot provides cost-effective and efficient transport solutions tailored for your smart factory needs.
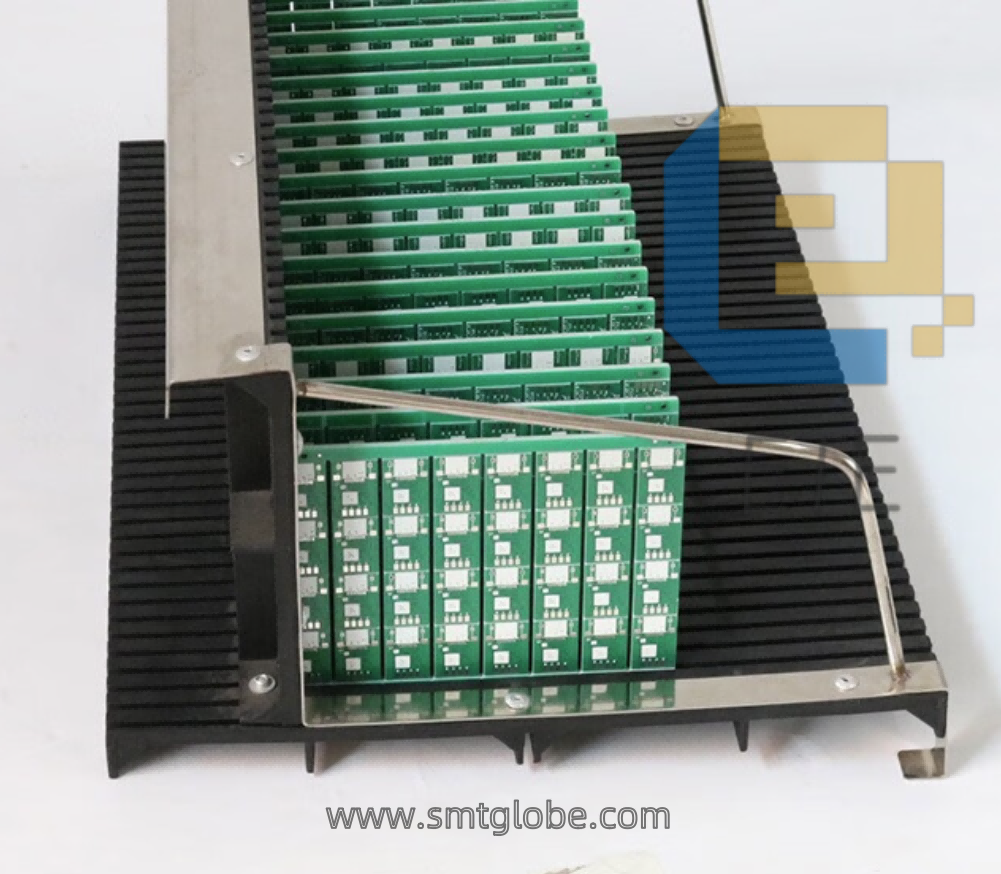
Introducing the ETE-AGV100-L
The ETE-AGV100-L is a groundbreaking AGV for PCB moving. With a robust loading capacity of 100KG, this AGV features self-guided driving and obstacle detection using ultrasound. It ensures seamless and safe material transport within smart factories.
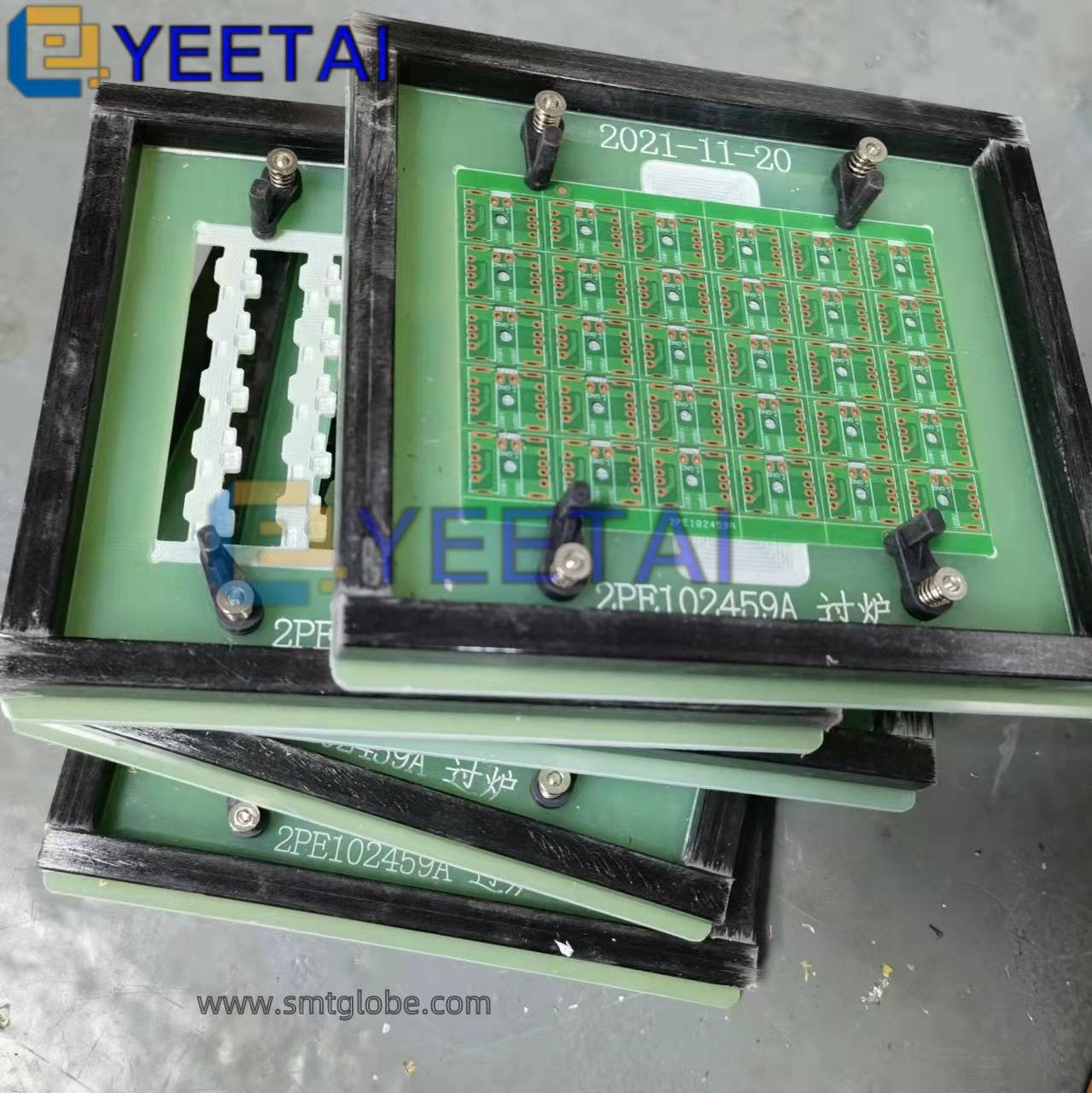
Key Features of the AGV for PCB moving
- Advanced Automatic Guidance System: Enables precise navigation within industrial settings.
- Autonomous Material Transport: Eliminates the need for manual intervention in handling processes.
- Versatile Operation: Effective in warehouses, manufacturing facilities, and distribution centers.
- Safety First: Built-in sensors and collision avoidance technology for a safe working environment.
- Programmable Routes: AGVs can follow specific paths, pick up and drop off materials at designated locations with minimal human interaction.
- Diverse Configurations: Available in various types, including forklift AGVs, tugger AGVs, and conveyor AGVs.
- Long-Lasting Battery: Powered by a high-capacity lithium battery with up to 10 hours of continuous runtime.
- Dual Charging Options: Charge directly on the AGV or remove the battery for charging.
- Automatic Charging Functionality: Optional feature available with an additional charging station.
- RFID Site Selection: Enables automated route setting for enhanced efficiency.
- High-Frequency DC Brushless Motor: Ensures reliable performance and durability.
- Comprehensive Safety Features: Equipped with ultrasonic and infrared sensors, and collision switches to detect obstacles and respond appropriately.
- Voice Notifications: The AGV issues clear audio alerts for operational updates.
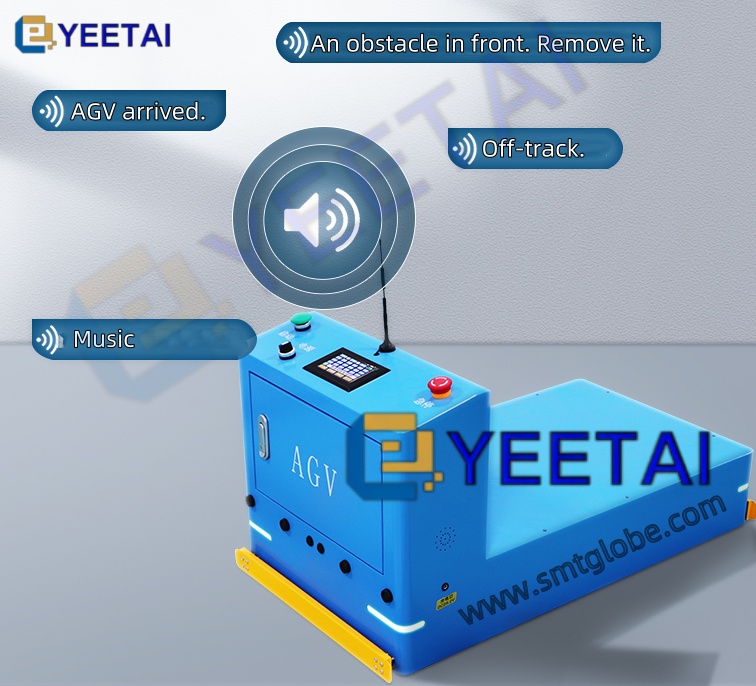

Specification
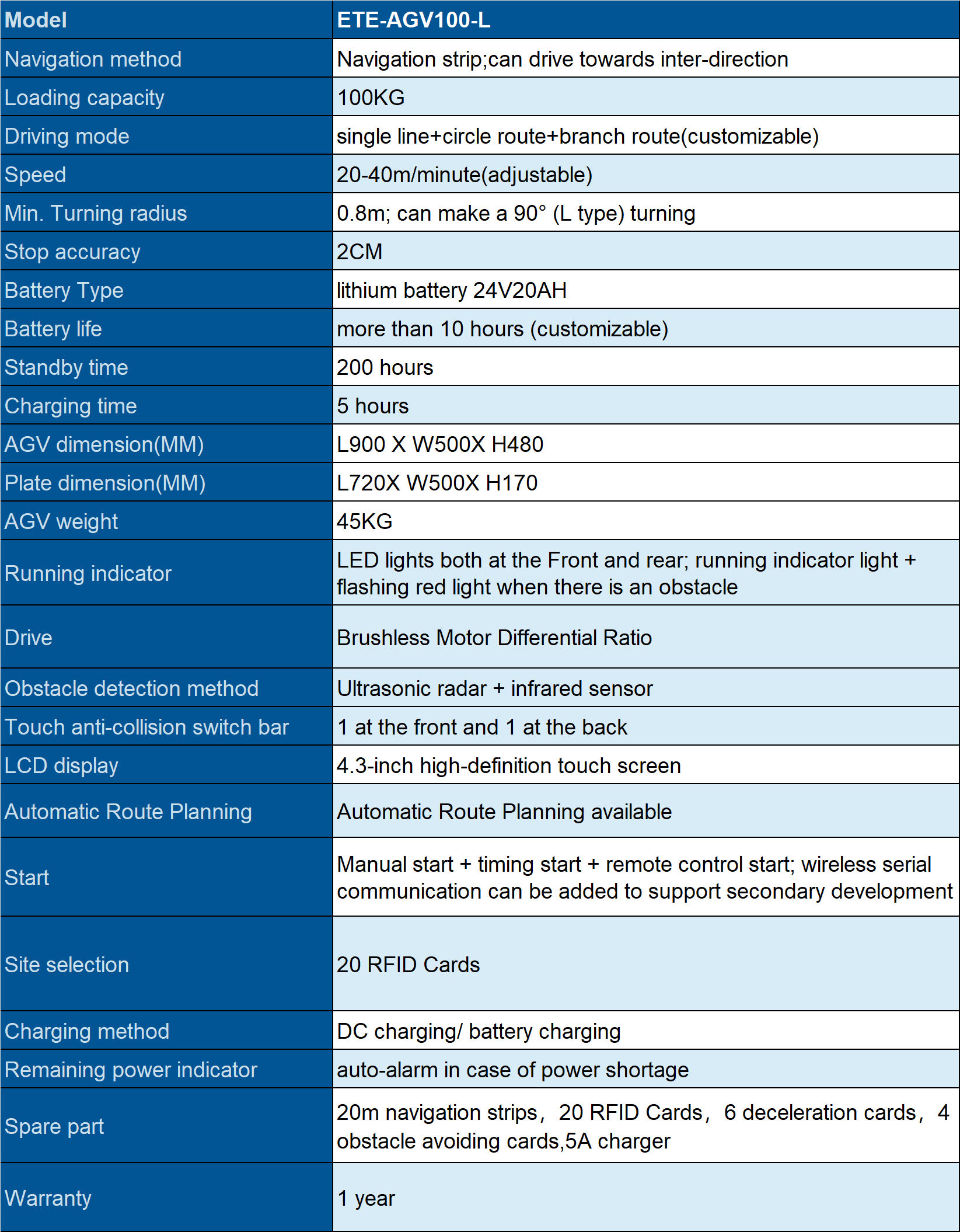
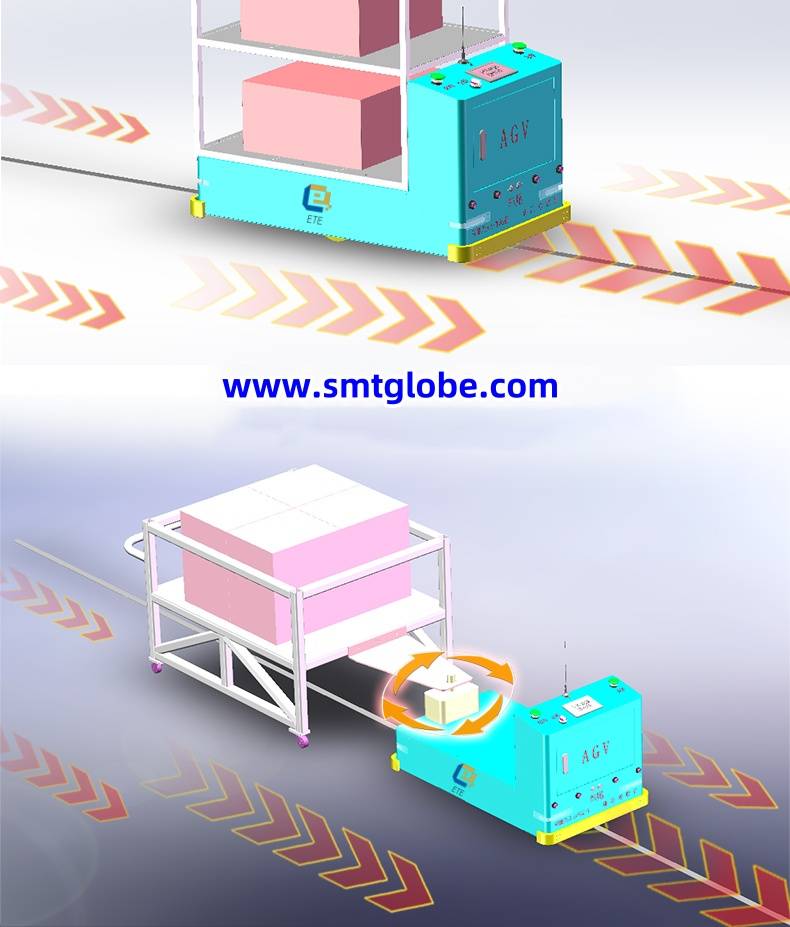
AGV Robust and Reliable Design
- Secure Connection: Custom shelving is designed for a tight fit with the AGV, preventing detachment.
- Intelligent Voice Alerts: High-quality speaker delivers clear and durable audio notifications.
- Premium Finish: The AGV body is crafted from high-quality steel, featuring a polished and refined surface for durability and aesthetics.
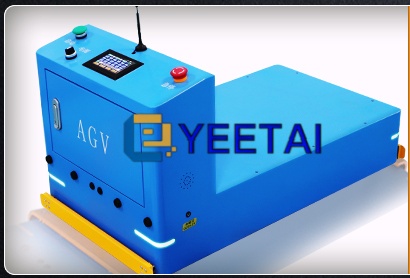
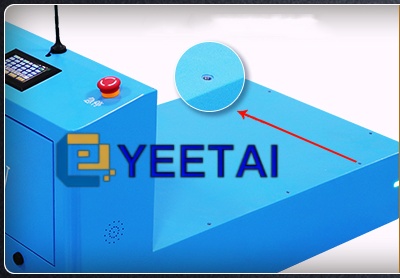
How to Install the Magnetic Navigation Strip for the AGV?
The AGV operates along a designated path marked by magnetic strips installed on the floor. Here’s how to properly install the magnetic navigation strip:
Installation Steps:
- Determine the Route: Confirm the AGV’s driving route and clean the installation area with a dry rag to remove any oil or grease.
- Prepare the Magnetic Strip: Tear off the backing paper, ensuring the S pole faces the ground and the smooth N pole is upward.
- Attach the Strip in a Straight Line: Two people are recommended for this task. One person holds one end while the other straightens the strip and removes the backing paper simultaneously.
- Create Circular Navigation Lines: Draw a circular arc on the ground (with a radius of at least 0.8 meters). Tear off the backing as you adhere the magnetic strip along the drawn arc.
How to Use the AGV for PCB moving
- Set the AGV Direction: Confirm the intended direction for the AGV.
- Drive in a Signal Line: Place RFID site cards along the magnetic strip, ensuring a distance of at least 1 meter between each site. For higher speeds, add speed-reducing cards 0.5 meters before and after turns to prevent the AGV from veering off course.
Why Choose the AGV for PCB in Your Manufacturing Needs?
Our AGV solutions are designed to enhance operational efficiency and safety in electronic manufacturing. With a focus on continuous innovation and customer collaboration, we offer tailored solutions that meet your specific material handling requirements.
Contact us today to learn more about how the ETE-AGV100-L can optimize your PCB transport and improve your production efficiency!