With the advancement of “machine replacing people” and “intelligent manufacturing,” the shift towards unmanned workshops has become a significant trend in the manufacturing sector. Automated Guided Vehicles (AGVs) are at the forefront of this transformation, providing efficient and unmanned transportation solutions embraced by numerous production enterprises. Let’s explore the key advantages that make AGV robots an appealing choice for smart manufacturing factories. Get started now.
1. Lower Cost
As AGV technology has developed and matured in recent years, the cost-effectiveness of these intelligent vehicles has significantly improved. With the diminishing demographic dividend and the continuous rise in labor costs, the advantages of transitioning to less labor-intensive or fully automated factories have become increasingly apparent. AGVs present a substantial reduction in ongoing operational costs compared to traditional human labor.
2. High Safety Standards
AGVs prioritize safety for both the vehicles themselves and the on-site personnel and equipment. They are equipped with multi-level hardware and software safety measures to ensure safe operation in various environments. This high level of safety enables factories to maintain a secure working atmosphere.
3. Increased Work Efficiency
In the SMT industry, AGVs enhance material handling processes, including loading and unloading, as well as transporting goods back and forth. They facilitate non-stop material changes, minimizing downtime and efficiently managing material usage to avoid inconsistencies that arise with manual operations. Furthermore, AGVs come with automatic charging features, allowing them to operate continuously for 24 hours, thus significantly boosting overall work efficiency.
4. High Reliability
Compared to manual handling, which often suffers from inefficiency and unpredictable factors such as the unknown routes and speeds of forklifts or trailers, AGVs provide greater control over navigation. Their paths and speeds are programmable, ensuring precise positioning and reliability in transporting materials. Additionally, AGV monitoring systems enable comprehensive oversight of each vehicle’s operation, further enhancing reliability.
5. Reduced Management Burden
In a factory with over 10,000 frontline workers, the combination of high labor intensity and low pay can lead to significant employee turnover and management challenges. The introduction of AGVs and intelligent robots facilitates the automation of labor management, improving the overall management level and effectively mitigating human factors that can disrupt productivity.
6. Flexibility and System Scalability
AGV management systems offer the flexibility to modify the paths of AGVs easily. Once tasks are assigned, the system can regulate traffic and adapt routes, providing excellent adaptability. Additionally, AGVs have become integral parts of the workflow, serving as vital links connecting various processes. This quality grants them considerable scalability, allowing industries to expand their automation solutions seamlessly.
Safety Features of AGVs
Visual and Auditory Alerts
AGVs are fitted with prominent signal lights and auditory alarms to alert nearby personnel of their presence, ensuring safe navigation within busy environments. In case of malfunctions, these robots automatically trigger visual and auditory alarms while wirelessly notifying the AGV monitoring system.
Collision Avoidance Systems
When multiple AGVs operate concurrently, the scheduling software includes safety protocols that enable them to work without interference. The AGV system can quickly address unexpected events while monitoring the overall activity of each vehicle.
Infrared Protection Sensors
Equipped with non-contact infrared sensors based on the principles of automotive bumpers, AGVs can detect obstacles within a certain range. If an obstacle is detected, AGVs will slow down and stop to avoid collisions, resuming normal operation only when the path is clear. This feature ensures that personnel or equipment encountering the AGV do not face injury or damage.
Conclusion
The application of intelligent AGV robots in the SMT industry underscores their role as a transformative force in modern manufacturing. By offering lower costs, enhanced safety, increased efficiency, and improved reliability, AGVs present a comprehensive solution to the challenges faced by traditional manufacturing processes. As factories increasingly embrace automation, AGVs are poised to become indispensable partners in the journey towards intelligent manufacturing, helping businesses thrive in an ever-evolving industrial landscape.
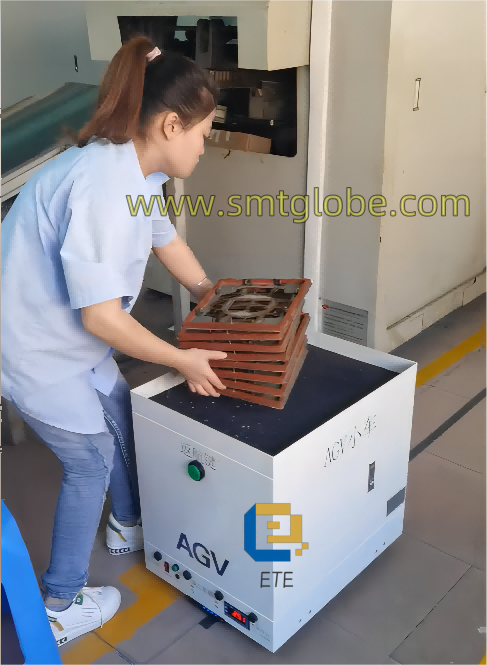
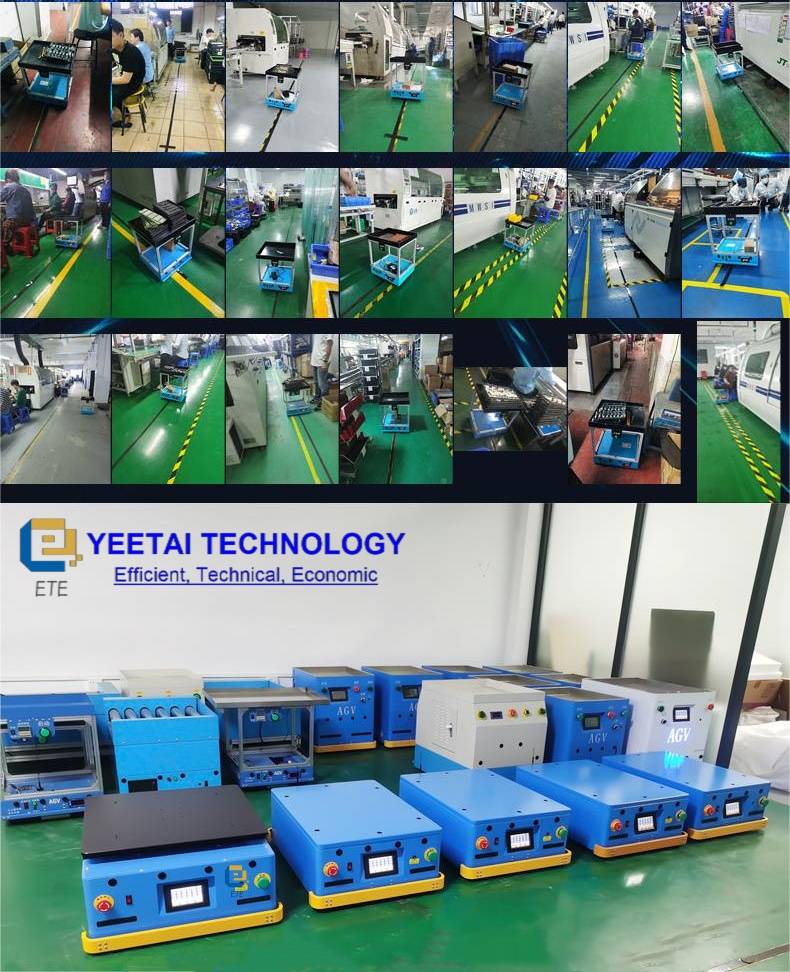
If you need any solutions, we are here to help.
Laser-guided SMT AGV Robot ETE-AGV-910A
SMT AGV Equipment for moving wave soldering pallet | ETE-AGV30-C
SMT Automatic Guided Vehicle ETE-AGV100-T
AGV for PCB moving | ETE-AGV100-L
Wave Soldering Pallet AGV | ETE-AGV60
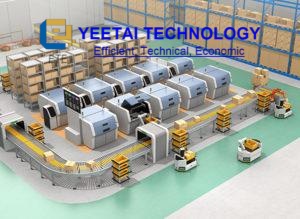