In the fast-paced world of electronic manufacturing, particularly within SMT (Surface Mount Technology) factories, efficiency and reliability are paramount. One of the key innovations that have revolutionized material handling in these environments is the Automated Guided Vehicle (AGV). This article explores the advantages of AGVs and how they can significantly enhance the transport of wave soldering pallets in SMT factories.You can know whether you need to implement such a machine.
What is an AGV?
An Automated Guided Vehicle (AGV) is a type of mobile robot equipped with automatic guiding devices such as electromagnetic or optical sensors. These vehicles navigate along predefined paths, ensuring safe and efficient transport without the need for a human operator. Typically powered by rechargeable batteries, AGVs are controlled via computer systems that dictate their routes and actions.
Key Advantages of AGVs
1. High Level of Automation
AGVs are designed for high levels of automation. They operate based on input from a computer system, which can receive requests from operators when materials are needed. For instance, when a specific component is required for production, a worker can input this information into the system. The AGV receives the command and autonomously transports the necessary wave soldering pallet to the designated location, streamlining the workflow and reducing manual labor.
2. Automated Charging
One of the standout features of AGVs is their ability to manage their own charging. When an AGV’s battery is running low, it sends a request to the system for charging. Once approved, the AGV will autonomously navigate to the charging station. This feature ensures that the AGV is always ready for operation, enhancing productivity. With a battery life of over two years and the ability to work for approximately four hours after just a 15-minute charge, AGVs minimize downtime.
3. Improved Aesthetics and Brand Image
AGVs not only enhance operational efficiency but also contribute to a modern and organized factory environment. Their sleek design can improve the overall aesthetic of the workspace, which can positively impact the company’s image. A well-organized facility can attract clients and enhance employee morale.
4. Space Efficiency
AGVs are designed to navigate through tight spaces, allowing them to operate in various areas of the production floor without requiring extensive real estate. This ability to move freely between different workstations reduces the need for large aisles and can maximize the use of available space in SMT factories.
5. Reliability and Safety
AGVs are equipped with advanced safety features, including sensors for obstacle detection and emergency stop capabilities. This reliability ensures that they can operate safely alongside human workers, reducing the risk of accidents and improving overall workplace safety.
AGV Navigation Methods
AGVs utilize several navigation methods that enhance their efficiency:
- Magnetic Guidance: AGVs equipped with magnetic sensors can detect small magnets embedded in the floor, allowing for precise path tracking.
- Electromagnetic Induction: This method involves buried wires that create an electromagnetic field. The AGV uses sensors to detect deviations from its path, ensuring stable and accurate navigation.
- Laser Guidance: AGVs with laser scanners can navigate by reflecting beams off highly reflective markers placed along their path. This method allows for more complex routing and is increasingly popular in modern AGV systems.
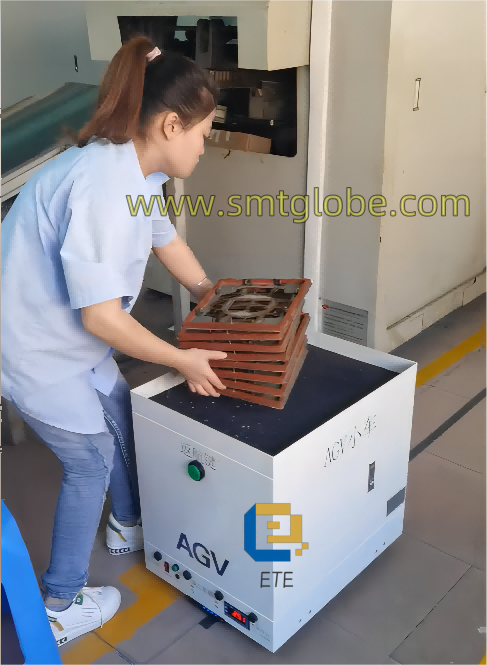
Conclusion
In the context of SMT factories, the advantages of AGVs are clear. They provide high levels of automation, efficient charging capabilities, aesthetic improvements, space efficiency, and enhanced safety. By implementing AGVs for the transport of wave soldering pallets, SMT manufacturers can optimize their operations, reduce labor costs, and improve overall productivity.
Investing in AGV technology not only streamlines material handling processes but also positions SMT factories for future growth and innovation. As the industry continues to evolve, AGVs will play a crucial role in maintaining competitive advantages in the electronic manufacturing landscape. By adopting AGVs, SMT factories can ensure that they remain at the forefront of efficiency and effectiveness in their operations.
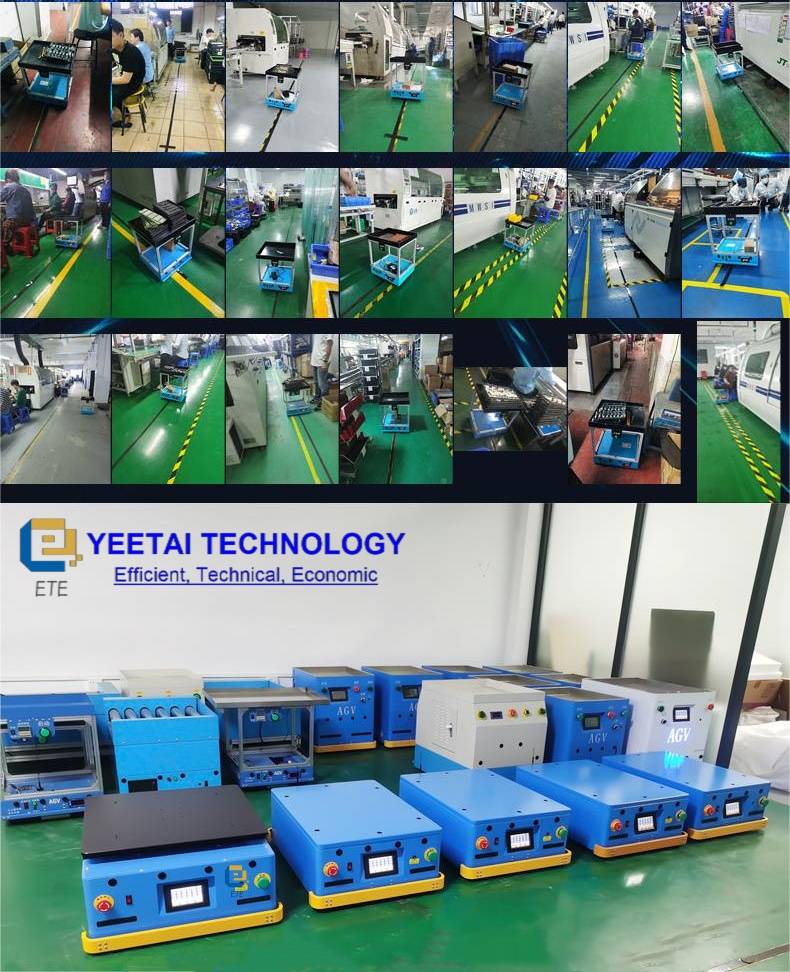
If you need any solutions, we are here to help.
Laser-guided SMT AGV Robot ETE-AGV-910A
SMT AGV Equipment for moving wave soldering pallet | ETE-AGV30-C
SMT Automatic Guided Vehicle ETE-AGV100-T
AGV for PCB moving | ETE-AGV100-L
Wave Soldering Pallet AGV | ETE-AGV60
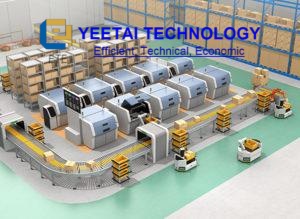